NOTE: Typical valve block shown
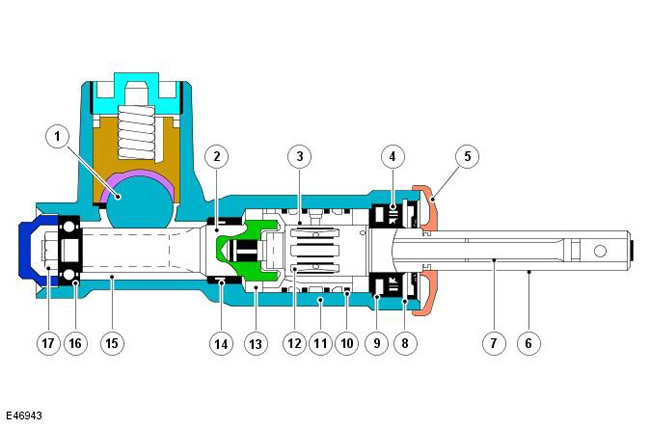
Pos. | spare part no | Name |
1 | - | Rail |
2 | - | gear shaft |
3 | - | Outer sleeve |
4 | - | oil sleeve |
5 | - | mud seal |
6 | - | input shaft |
7 | - | Torsion |
8 | - | Retaining ring |
9 | - | Oil seal |
10 | - | PTFE ring (PTFE) |
11 | - | Steering gear housing |
12 | - | grooves |
13 | - | Pin - gear shaft to outer sleeve |
14 | - | Oil seal |
15 | - | gear shaft teeth |
16 | - | Bearing |
17 | - | Gear Shaft Nut |
The valve block is an integral part of the steering gear. The main function of the valve block is to optimize the effort on the steering wheel due to the operation of the hydraulic booster (e.g. when parking). The steering gear housing is an integral part of the steering gear assembly.
The steering gear housing has four ports for connecting the pressure line from the power steering pump, the return line to the reservoir, and the pressure lines to each side of the piston. The non-return valve and seal are installed in the opening for the pressure line coming from the power steering pump. The valve block consists of an outer sleeve, an input shaft, a torsion bar and a pinion shaft.
The valve block is on the same axis as the gear shaft, which is connected to the steering column through the input shaft. The elements of the valve block are located in the steering gear housing with a sealed cover. The outer sleeve is located in the main bore of the gear housing. Three annular grooves are made along its outer diameter. Fluoroplastic rings are installed between the grooves, which seal the hole in the gear housing. In each annular groove, radial holes are drilled through the bushing wall. The axial bore of the outer sleeve is bored to fit the input shaft. Six grooves are machined in the bushing hole at an equal distance from each other.
The ends of the grooves are closed and do not come out. Radial holes in the outer sleeve are drilled into each slot. The input shaft has two machined flats at its outer end which allow the yoke of the intermediate steering column shaft to be attached. The planes ensure that the intermediate shaft is in the correct position to maintain the optimum phase angle. The inner end of the input shaft has a lip that mates with a slot in the pinion shaft. The position of the lip in the slot allows for a slight relative rotation of the input shaft and the pinion shaft before the lip touches the slot wall. This makes it possible, in the event of a hydraulic booster failure, to use the steering manually, while avoiding excessive loads on the torsion bar.
Along the circumference of the central part of the input shaft, longitudinal grooves are machined at an equal distance from each other. The slots are arranged alternately around the input shaft. The torsion bar is attached to the inside of the input shaft and to the pinion shaft. The torsion bar is connected to the input shaft by means of a drive pin. In the central part, the torsion bar has a smaller diameter than at the ends. The smaller diameter allows the torsion bar to twist under the torque applied to the steering wheel, depending on the grip of the tires on the road surface. The gear shaft has a protrusion in the center, which is mated with a protrusion on the steering rack. A groove machined in the top of the pinion shaft accepts a lug on the input shaft. The gear shaft is located in the gear housing and rotates on ball bearings.
Comments on this article