Steels are divided into several groups according to tensile strength and yield strength (force required to plastically deform a material).
Yield strength
The yield strength determines the force at which the metal loses its elasticity and begins to plastically deform without subsequent restoration of shape.
Tensile strength
The tensile strength determines the force at which the tensile specimen breaks.
Duplex steel (DP) may meet both the VHSS classification and the EHSS classification, depending on the brand.
steel grade | Yield strength |
Mild low carbon steel (MS) | Yield strength up to 180 MPa |
high strength steel (HSS) | Steel with yield strength up to 280 MPa |
High-strength steel with increased yield strength (VHSS) | Steel with yield strength up to 380 MPa |
Heavy Duty Steel (EHSS) | Steel with yield strength up to 800 MPa |
Ultra strong steel (UHSS) | Steel with yield strength over 800 MPa |
Ultra high strength steel welding
Welding ultra high strength steel requires the use of welding equipment capable of the following welding parameters.
Hard soldering in an inert gas environment
When performing inert gas brazing, use the following type of welding machine that meets the specified specification: Fronius Trans Plus Synergic 2700 4 R/Z/AL MIG welding machine, with CuSi3 wire (DIN 1733) with a diameter of 1.0 mm and using step 4, which corresponds to a current of 92 A and a feed speed of 4.6 m/min. Shielding gas L1 = pure argon (DIN 439).
Steels used in body construction:
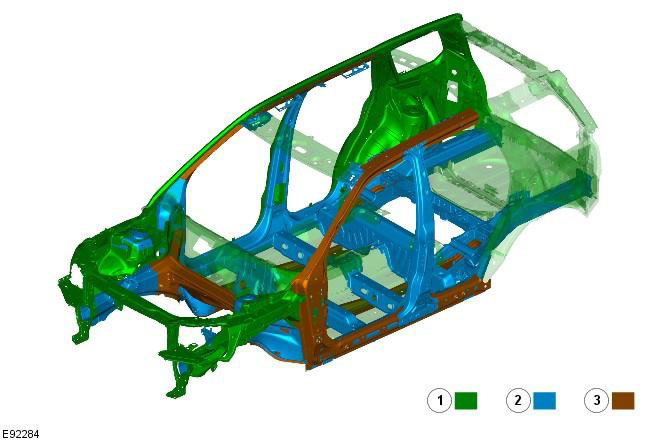
Element | steel grade |
1 | Soft (low carbon) steel (SS) |
2 | high strength steel (HSS) |
3 | Heavy Duty Steel (EHSS) |
NOTE: Optional use of DP600 steel (EHSS) V "ring frame" reinforcements in the side panels and in the rear and front side members provide greater strength in a frontal or side impact.
NOTE: When installing the outer side panels, racks "A", "IN", sill panel and rear side panel, the grooves must be hard soldered where these elements meet their internal reinforcing panels.
NOTE: Groove size 20mm x 8mm, distance between grooves 30mm. Grooves should be made in accordance with this interval. Where this is not possible due to dents in the panel, a groove should be made at the location of the original spot weld.
Side panel
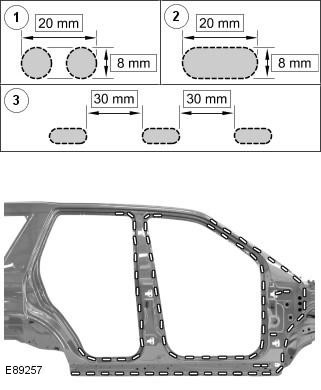
Element | Name |
1 | To make the base for the groove, drill 2 8mm holes. |
2 | Make a groove of 20mm x 8mm |
3 | The distance between the grooves should be 30mm |
NOTE: Brazing in a protective atmosphere is carried out at a temperature of 650°C - 950°C. In order for ultra-strong steel not to lose its properties, the temperature should not exceed 950°C.
Braze the grooves with the Fronius Trans Plus Synergic 2700 4 R/Z/AL MIG welding machine, with CuSi3 wire (DIN 1733) with a diameter of 1.0 mm and using step 4, which corresponds to a current of 92 A and a feed speed of 4.6 m/min. Shielding gas L1 = pure argon (DIN 439).
Sand the overlay in the groove with a belt sander using a 60/80 grit belt.
Comments on this article