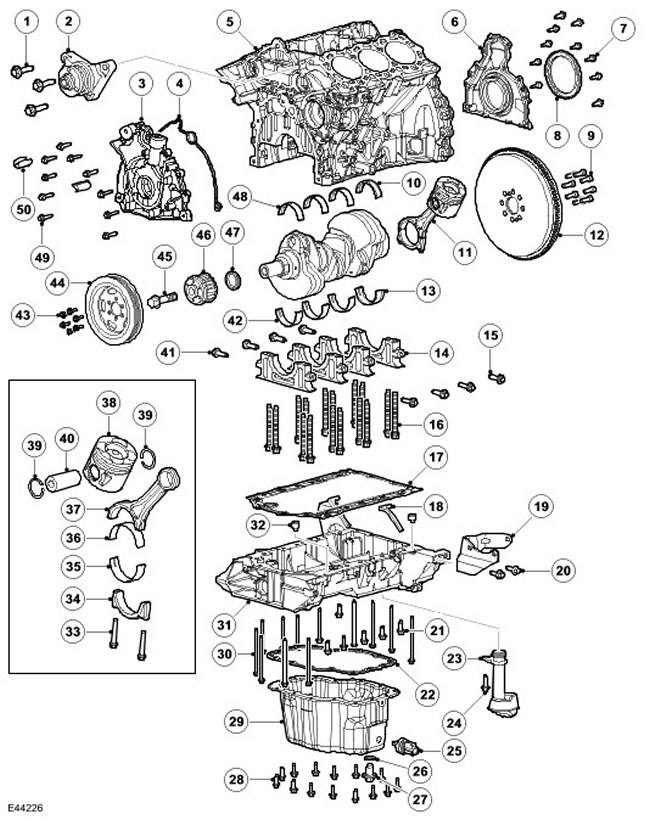
Item name | Spare part number | Description |
1 | - | Bolts, 3 pcs. |
2 | - | Fan drive bracket |
3 | - | Oil pump |
4 | - | Seal |
5 | - | Cylinder block |
6 | - | Rear oil seal holder |
7 | - | Bolts, 10 pcs. |
8 | - | Crankshaft position sensor target |
9 | - | Bolts, 8 pcs. |
10 | - | Main thrust bearing, upper |
11 | - | Piston with connecting rod assy |
12 | - | Flywheel |
13 | - | Main thrust bearing, lower |
14 | - | Main bearing caps, 4 pcs. |
15 | - | Cross bolts, 4 pcs. |
16 | - | Main bearing cap bolts, 16 pcs. |
17 | - | Pad |
18 | - | Seal |
19 | - | bracket |
20 | - | Bolts, 2 pcs. |
21 | - | Bolts, 6 pcs. |
22 | - | Pad |
23 | - | Oil pickup tube |
24 | - | Bolt |
25 | - | Oil temperature sensor |
26 | - | Seal |
27 | - | drain plug |
28 | - | Bolts, 14 pcs. |
29 | - | Oil pan assembly |
30 | - | Bolts, 12 pcs. |
31 | - | Stair construction |
32 | - | Pin |
33 | - | Bolts, 2 pcs. |
34 | - | Connecting rod cap |
35 | - | Connecting rod bearing cap |
36 | - | Connecting rod bearing |
37 | - | connecting rod |
38 | - | Piston |
39 | - | Piston pin holder |
40 | - | piston pin |
41 | - | Cross bolts, 4 pcs. |
42 | - | Lower main bearings |
43 | - | Bolts, 5 pcs. |
44 | - | Crankshaft damping clutch pulley |
45 | - | Bolt |
46 | - | crankshaft drive pulley |
47 | - | Front crankshaft oil seal |
48 | - | Upper main bearings |
49 | - | Bolts, 10 pcs. |
50 | - | Seal |
Crankshaft
The crankshaft is made of forged steel with fillet rolled and induction hardened journals, fitted with four bearings with clamping double-layer liners.
The main bearing caps are double bolted, which gives extra strength and rigidity to the cylinder block.
The crankshaft drive pulley is attached to the shaft not with a key, but with one bolt.
NOTE: Under no circumstances should the crankshaft pulley be tightened or loosened with the timing belt installed.
NOTE: Do not attempt to remove the crankshaft pulley unless you have the correct crankshaft locking tool.
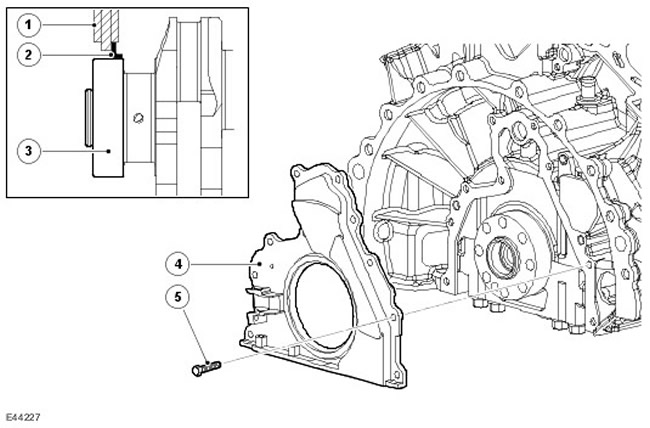
Item name | Spare part number | Description |
1 | - | Frame |
2 | - | Seal |
3 | - | Crankshaft |
4 | - | Rear oil seal holder |
5 | - | Bolt |
The crankshaft rear oil seal is pressed into the rear oil seal holder. A CKP sensor is also installed in the rear oil seal holder.
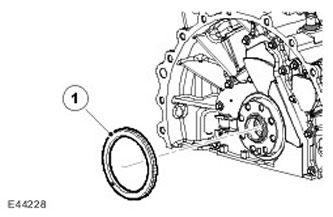
Item name | Spare part number | Description |
1 | - | CKP sensor target |
The target is located at the rear of the crankshaft. The target is pressed onto the crankshaft using a special tool, which also ensures accurate target placement for correct crankshaft position and valve timing. The target consists of 60 minus 2 magnets for the ECM to determine the position of the crankshaft and synchronize. The magnets on the target are not visible, so the correct positioning of the target can only be done with a special tool.
The air gap of the CKP sensor is 0.4-0.5 mm and does not need to be adjusted. The sensor is bolted to the rear oil seal holder and the tolerances on the holder and sensor provide the required air gap.
NOTE: If a target is removed for any reason, a new target must be installed. Do not reuse an old target.
Main bearings
Selected aluminum/tin split bearings are used as main bearings. An oil groove in the top half of each bearing supplies engine oil to the crankshaft to lubricate the connecting rod bearings. Thrust washers are mounted in the upper and lower shells of the fourth bearing, which limit the axial play of the crankshaft.
Stair construction
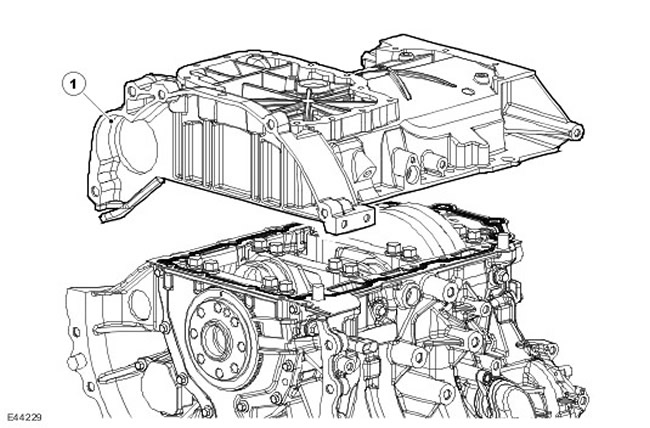
Item name | Spare part number | Description |
1 | - | Stair construction |
Ladder structure mounted on the cylinder block increases engine rigidity and reduces noise, mechanical vibrations and low-frequency vibration (NVH). Die cast aluminum construction includes an oil deflector to reduce foaming and oil splashing.
The ladder structure is attached to the cylinder block with 2 pins, 2 alignment pins for gasket and 18 mounting bolts, using three bolt lengths:
- M6 x 20 x 6
- M8 x 75 x 4
- M6 x 105 x 8
Iron inserts molded into the ladder main bearing housings ensure minimal change in bearing clearance due to thermal expansion.
The joint between the ladder structure and the cylinder block is sealed with a gasket.
In the casting on the left side of the structure there is a channel for the dipstick tube.
An oil pick-up tube with an internal strainer is located in the front of the structure, which provides oil to the crankshaft-driven oil pump.
Oil pan
The sump is made of pressed steel and is attached to the aluminum alloy ladder structure with 14 M6 x 16 bolts. The engine oil drain plug and oil temperature sensor are located in the left rear corner of the oil sump.
A reusable gasket is provided to seal the joint between the oil pan and the ladder structure; a sealant is used to seal the joint between the oil pan and the ladder structure.
Oil temperature sensor
The engine oil temperature sensor is mounted in the left rear corner of the oil pan. This sensor reports the engine oil temperature to the ECM and instrument cluster.
The sensor circuit includes an internal voltage divider circuit, which includes an NTC thermistor (NTC). As the engine oil temperature rises, the resistance of the sensor decreases, and vice versa. The output of the sensor is the change in voltage due to the increase in current flowing through the thermistor to ground in response to the change in oil temperature. For more information refer to Electronic Engine Controls (303-14C Electronic Engine Controls - 2.7L Diesel).
Rear oil seal holder
The crankshaft rear oil seal holder is secured with 10 bolts to the rear of the cylinder block through a rubber seal. The crankshaft position sensor is mounted in the holder.
Double flywheel
On vehicles with a manual transmission, a dual flywheel is attached behind the crankshaft with 8 bolts. The key on the crankshaft flange ensures the correct position of the flywheel. A ring gear is installed on the surface of the outer diameter of the flywheel. The ring gear is maintenance free.
The dual flywheel protects the transmission from transient and torsional vibrations generated by the engine. For more information refer to Clutch (308-01 Clutch - 2.7L Diesel).
Comments on this article