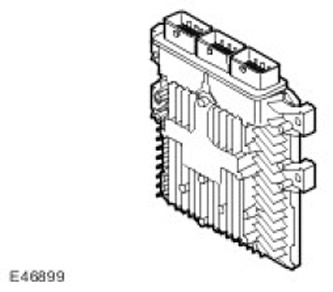
ECM (the engine control unit) located in the mounting box in the chamber on the right side of the engine compartment, fixed to the bulkhead.
Mounting box
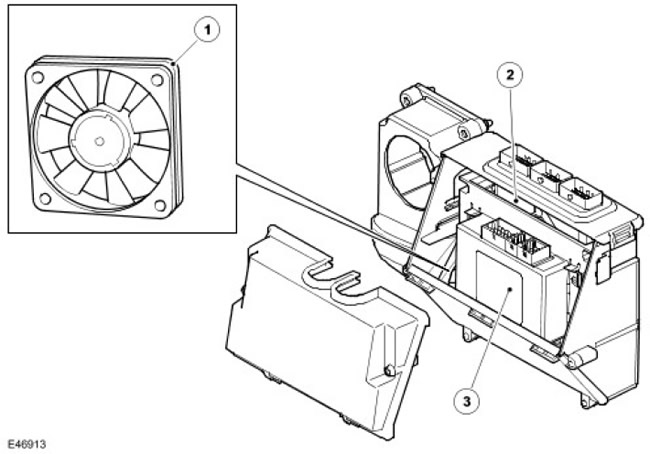
Item name | Spare part number | Description |
1 | Control junction box fan | |
2 | ECM (the engine control unit) | |
3 | Transfer box controller |
Input signals
To ECM input (the engine control unit) the following signals are received:
- Coolant temperatures
- clutch switch (via parking brake controller)
- Stoplight switch (via the ABS control unit (anti-lock brakes) via CAN bus (local area network of controllers))
- Manifold absolute pressure
- Accelerator pedal positions 1
- Accelerator pedal positions 2
- Electronic throttle positions
- Viscous fan speeds
- Position and engine speed sensor (crankshaft sensor)
- Camshaft position sensor
- Engine oil temperatures
- cruise control speed switches (resistive ladder chains)
- Vehicle speeds (via CAN bus (local area network of controllers))
- Generator control circuits
- Airbag and seatbelt system module
- Manifold absolute pressure and intake air temperature
Output signals
ECM block (the engine control unit) generates output signals to control the following components and parameters:
- Throttle actuator
- nozzles (6 items)
- EGR valves (exhaust gas recirculation systems)
- Cooling fan
- Fuel pump relay
- Starter relay
- A/C Condenser Fan Module
- EMS Power Relay
- Control of the viscous coupling of the fan of the cooling system
- Generator control
To on-board network ECM (the engine control unit) connected via three connectors. In ECM (the engine control unit) contains processors and memory microchips. Actuator outputs are provided by grounding loops with ECM control circuits (the engine control unit). ECM control circuits (the engine control unit) generate heat during normal operation and dissipate it through the housing. The fan in the electronic box contributes to the cooling process by maintaining a constant temperature in the box. The fan is controlled by a thermal switch located in the mounting box. The junction box is connected to the interior of the vehicle and receives additional cooled air through the A/C system. Some sensors receive a regulated voltage supplied by the ECM (the engine control unit). This measure avoids signal distortion caused by a voltage drop when the engine is cranked by the starter.
ECM (the engine control unit) carries out self-diagnosis procedures and writes fault codes in memory. These DTCs and diagnostics can be accessed using the Land Rover approved diagnostic system. If ECM (the engine control unit) needs to be replaced, new ECM (the engine control unit) must be configured using a Land Rover approved diagnostic system as it is shipped unprogrammed. Electrically Erasable Programmable Read Only Memory EEPROM (flash memory) Allows up to 14 ECM configurations with Land Rover approved diagnostic system (the engine control unit) according to market specifics or new regulatory information. If the 15th program update is required, the ECM (the engine control unit) must be replaced. Current engine settings can be retrieved and read using the Land Rover approved diagnostic system.
When installing a new ECM (the engine control unit) it must also be synchronized with the theft deterrent control module using a Land Rover approved diagnostic system. Can't swap ECM (the engine control unit) different cars.
ECM (the engine control unit) is connected to engine sensors that allow it to control the engine's operating mode. ECM (the engine control unit) processes the sensor signals and decides what actions need to be taken to maintain optimal engine performance in terms of overall vehicle drivability, fuel efficiency and exhaust emissions. To ECM memory (the engine control unit) when programming, instructions are entered with an engine control algorithm called a control strategy. In addition, the memory contains data in the form of special tables, based on which the ECM (the engine control unit) supplies fuel and reduces exhaust emissions. By comparing information from sensors with data from ECM tables (the engine control unit) is able to form the requirements for the operation of different systems. ECM (the engine control unit) contains an adaptive strategy that updates the system when its elements undergo changes due to technological tolerances or aging.
ECM (the engine control unit) receives vehicle speed signal via CAN bus (local area network of controllers) from the ABS control module (anti-lock brakes). Vehicle speed is an important input to ECM strategies (the engine control unit). ABS control module (anti-lock brakes) determines the speed signal based on the signals from the ABS wheel speed sensors (anti-lock brakes). The frequency of these signals depends on the speed of movement. ECM (the engine control unit) uses this signal to determine the following:
- How much to reduce engine torque when shifting gears.
- When to enable speed control operation.
- To control the operation of the speed control system.
- Idling mode control on a stationary vehicle.
C0872 ECM harness connector pins
contact no | Purpose | Input signal / output signal |
A1 | Serial communication line with immobilizer control unit | Output signal |
A2 | Serial communication line with immobilizer control unit | Input signal |
A3 | CAN bus low signal (local area network of controllers) | Input signal / output signal |
A4 | CAN bus signal high (local area network of controllers) | Input signal / output signal |
B1 | Starter enable | Output signal |
B2 | APP sensor weight (accelerator pedal position) | - |
B3 | Mass of the temperature sensor at the outlet of the radiator | - |
B4 | Cruise control | Input signal |
C1 | APP sensor weight (accelerator pedal position) 1 | - |
C2 | APP sensor reference voltage (accelerator pedal position) 2 | Output signal |
C3 | ECT sensor (coolant temperature) | Output signal |
C4 | Cruise control | Input signal |
D1 | APP sensor signal (accelerator pedal position) 1 | Input signal |
D2 | APP sensor weight (accelerator pedal position) 2 | - |
D3 | Voltage 2 | Input signal |
D4 | Not used | - |
E1 | APP sensor reference voltage (accelerator pedal position) 1 | Output signal |
E2 | Water in fuel sensor | Input signal |
E3 | Brake switch 1 | Input signal |
E4 | Inertial switch | Input signal |
F1 | Intake air temperature sensor | Input signal |
F2 | Not used | - |
F3 | Engine crank signal | Input signal |
F4 | Mass air flow sensor. | Input signal |
G1 | Fuel pump power control | Input signal |
G2 | Stoplight switch | Input signal |
G3 | Not used | - |
G4 | Not used | - |
H1 | Not used | - |
H2 | Not used | - |
H3 | Not used | - |
H4 | Not used | - |
J1 | Not used | - |
J2 | Control junction box fan | Output signal |
J3 | Power relay | Output signal |
J4 | Fuel pump relay | Output signal |
K1 | Not used | - |
K2 | Electric cooling fan control | Output signal |
K3 | Ignition sensor | Input signal |
K4 | Standby Power | Input signal |
L1 | Battery voltage | Input signal |
L2 | Battery voltage | Input signal |
L3 | Battery voltage | Input signal |
L4 | Weight | - |
M1 | Weight | - |
M2 | Weight | - |
M3 | Weight | - |
M4 | Weight | - |
C0411 ECM Wiring Harness Connector Pins
contact no | Purpose | Input signal / output signal |
A1 | Engine oil temperature sensor | Input signal |
A2 | Not used | - |
A3 | Not used | - |
A4 | Not used | - |
B1 | Reserve analog input | Input signal |
B2 | Reserve analog input | Output signal |
B3 | CAN bus low signal (local area network of controllers) | Input signal / output signal |
B4 | CAN bus signal high (local area network of controllers) | Input signal / output signal |
C1 | Not used | Input signal |
C2 | Sensor weight | |
C3 | Not used | |
C4 | Bank B knock sensor (-) | Input signal |
D1 | Rail pressure sensor signal | Input signal |
D2 | Fuel rail pressure sensor | Output signal |
D3 | Bank B knock sensor (+) | Output signal |
D4 | Bank A knock sensor (-) | Input signal |
E1 | Throttle position sensor | Input signal |
E2 | Ground pressure sensor in the fuel rail | - |
E3 | Glow plug supply control, bank A | Input signal |
E4 | Bank A knock sensor (+) | Input signal |
F1 | Electronic throttle voltage | Output signal |
F2 | Weight of electronic throttle | - |
F3 | Bank B Glow Plug Monitoring | Input signal |
F4 | Reserved PWM output (pulse width modulation) | Output signal |
G1 | Active engine mount control 1 | Output signal |
G2 | Active engine mount control 2 | Output signal |
G3 | Glow plug relay control | Output signal |
G4 | Not used | - |
H1 | Generator command | Output signal |
H2 | Not used | - |
H3 | Not used | - |
H4 | Not used | - |
J1 | Not used | - |
J2 | Control junction box fan | |
J3 | Power relay | Output signal |
J4 | Fuel control valve | Output signal |
K1 | Mass of engine oil temperature sensor | - |
K2 | Viscous fan control | Output signal |
K3 | Fuel pressure control valve | Input signal |
K4 | Inlet Port Shutoff Actuator | Output signal |
L1 | Injector command 1 | Output signal |
L2 | Common nozzle 1 | - |
L3 | Common nozzle 3 | - |
L4 | Output signal | |
M1 | Injector command 3 | Output signal |
M2 | Injector command 5 | Output signal |
M3 | Common injectors 5 | - |
M4 | Weight 7 | - |
Connector pins C2518 ECM wiring harness
contact no | Purpose | Input signal / output signal |
A1 | Reserve analog input | - |
A2 | EGR valve position sensor (exhaust gas recirculation systems) row B | Input signal |
A3 | EGR valve position sensor (exhaust gas recirculation systems) row A | Input signal / output signal |
A4 | Not used | Input signal / output signal |
B1 | charge air temperature sensor | Input signal |
B2 | Fuel temperature sensor | Input signal |
B3 | Not used | - |
B4 | Not used | - |
C1 | Manifold absolute pressure sensor | Input signal |
C2 | Engine coolant temperature sensor | - |
C3 | Analog voltage 1 | Input signal |
C4 | VGT row A | Input signal |
D1 | Manifold absolute pressure sensor power supply | Output signal |
D2 | Sensor weight M | Output signal |
D3 | Not used | |
D4 | Not used | |
E1 | Engine cooling fan monitor | Input signal |
E2 | Not used | - |
E3 | Not used | - |
E4 | Not used | - |
F1 | crankshaft position sensor | Input signal |
F2 | Generator Load Sensor Signal | Input signal |
F3 | Not used | - |
F4 | Not used | - |
G1 | Crankshaft Position Sensor Power | Output signal |
G2 | Mass of the crankshaft position sensor | - |
G3 | Variable geometry turbine drive weight | - |
G4 | Camshaft sensor signal | Input signal |
H1 | EGR (exhaust gas recirculation systems) row A (+) | Output signal |
H2 | EGR (exhaust gas recirculation systems) row A (-) | - |
H3 | Weight of camshaft position sensor | - |
H4 | Camshaft Position Sensor Power | Output signal |
J1 | EGR (exhaust gas recirculation systems) row B (+) | Output signal |
J2 | VGT row A (+) | Output signal |
J3 | Not used | Output signal |
J4 | Throttle actuator (+) | Output signal |
K1 | EGR (exhaust gas recirculation systems) row B (-) | - |
K2 | VGT (-) | - |
K3 | Not used | Input signal |
K4 | Throttle actuator (-) | - |
L1 | Not used | - |
L2 | Common injectors 2 | - |
L3 | Common injectors 0 | - |
L4 | Common injectors 4 | - |
M1 | Power circuit ground | - |
M2 | Injector command 2 | Output signal |
M3 | Injector command 0 | Output signal |
M4 | Nozzle command 4 | Output signal |
Unauthorized start blocking
The IMMOBILIZER control unit receives data from the relevant vehicle systems and transmits a coded signal to the ECM (the engine control unit) to allow the engine to start if all the conditions for doing so are met. Data is decoded by ECM (the engine control unit), and if they are true, the engine starts.
The data is a continuously changing code, so the immobilizer control unit and ECM (the engine control unit) must be synchronized in case of replacement of any of the devices.
In addition, ECM (the engine control unit) protects the starter from accidental operation. The IMMOBILIZER control unit receives the engine speed signal from the ECM through the instrument cluster (the engine control unit). If the engine speed exceeds the preset value, the immobilizer control unit disables the starter operation by means of the built-in starter blocking relay. For more information refer to AntiTheft - Passive (419-01B Anti-Theft - Passive)
Comments on this article