General information
Care must be taken to maintain the anti-corrosion coating applied during the manufacture of the vehicle and / or restore the protective layer during and after body repair work. Only in this case, conditions are provided that prevent through corrosion.
Only Genuine Land Rover body parts and materials may be used for body repairs (sealants, paint, etc.), licensed for use by this company.
Genuine Land Rover Parts
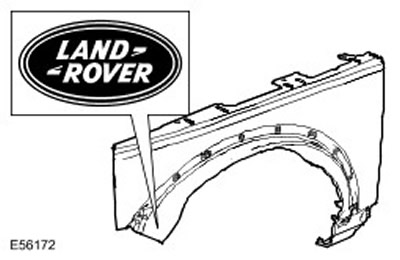
All Land Rover body repair parts are cathodic coated. Individual body parts galvanized on one or both sides (in different areas depending on the car model).
Together with the elastic paint coating, this guarantees optimal high protection against corrosion caused by impacts from small objects such as gravel.
NOTE: Individual protective covers (galvanized, cathodic coating) should not, as far as possible, be damaged or destroyed by sandblasting or other mechanical operations.
If after straightening work in the joint area of body parts (e.g. around door hinges) hair-like cracks appear, then it is necessary to restore the protection against corrosion at the level provided by the factory technology. If necessary, completely restore the paintwork. The same applies to straightening complex profiles (e.g. floor panel). If necessary, renew or refresh the paintwork, sealant bead and underbody protection.
After repair, primer should be applied to all internal surfaces that will not be visible or accessible before applying cavity wax. Thoroughly spray the entire cavity to ensure an even coating of the inner surfaces (twice, with intermediate drying).
If the body panels are subjected to intense heat during the repair process, this invariably leads to damage or even destruction of the structure of the anti-corrosion coating. Heat reduces the effectiveness of the cavity protection material. Therefore, it is imperative to re-treat the damaged areas.
Weld seams must be cleaned before applying the anti-corrosion protective coating.
Corrosion protection measures to be taken when replacing body parts are described on the following pages.
Corrosion protection for new parts
All new components should be checked for shipping damage such as scratches or dents. Depending on the extent of damage, the following operations may be necessary:
Undamaged new part
- Do not scrape the cathodic primer.
- Thoroughly clean the surface with silicone remover and wipe dry.
Slightly damaged new part
- Sand the scratches
- Sand the surrounding area carefully.
- Thoroughly clean the surface with silicone remover and wipe dry.
- Apply an anti-corrosion primer to the cleaned areas.
Damaged new parts (bulges and dents)
- Sandblast the dented areas down to metal.
- Apply polyester filler (only on bare metal surfaces)
- Apply putty.
- Lightly sand the entire piece.
- Thoroughly clean the surface with silicone remover and wipe dry.
- Apply an anti-corrosion primer to the cleaned areas.
Welding elements
Using a rotating wire brush, remove the coating from the inside and outside of the area to be welded. Be careful not to damage the zinc coating when doing this.
NOTE: The areas to be sanded should be as small as possible and the anti-corrosion coating applied at the time of manufacture of the vehicle (cathodic soil), should be preserved as much as possible.
NOTE: The welding primer must be well mixed before application.
Thoroughly clean the repair area (silicone remover).
Apply welding primer evenly to all flanges to be welded (old and new).
NOTE: The welding primer must be dry before welding.
Apply welding primer
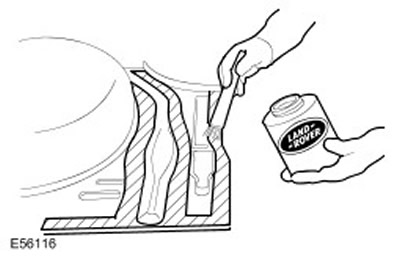
Weld beads should be removed after welding, being careful not to weaken the material.
All irregularities in the weld must be removed.
If necessary, spot weld the missing T-pins to secure the trim tape clips in position. To avoid corrosion, the car should be completely cleaned of abrasive dust and metal chips.
Clean and prime all interior areas and areas to be sealed.
NOTE: The primer must be dry before applying sealant or underbody protection. Do not use solvents when applying sealant (sealant will not dry).
Partial replacement
For partial replacement of components, follow the procedure described in section «Elements to be welded».
The main difference between a partial replacement of components and a complete replacement is the preparation of butt welds and lap joints.
- When cutting body parts, care must be taken to properly remove paint and zinc coating on interior areas. This primarily applies to hard-to-reach interior areas.
- To ensure the quality of the weld, it is important that the inside surface be cleaned down to metal. Residues of zinc and paint coating in the area of the weld burn out and form significant gaps during welding.
- If the zinc layer and paintwork is not removed, the zinc and paint will burn during the welding process. The resulting soot prevents proper cavity protection.
Sequencing
- Remove a 30 mm wide area of paint along the weld line with a rotating wire brush.
- This operation should be performed on new and old body parts.
- Depending on the bodywork element, the lower zinc layer must also be removed in a 10 mm wide area along the weld line.
NOTE: If the cavity is small, a flat squeegee or wire brush can be used instead of a rotating brush. Do not use an angle grinder as this may weaken the structure.
Application of cavity wax on door sill panel after partial repair
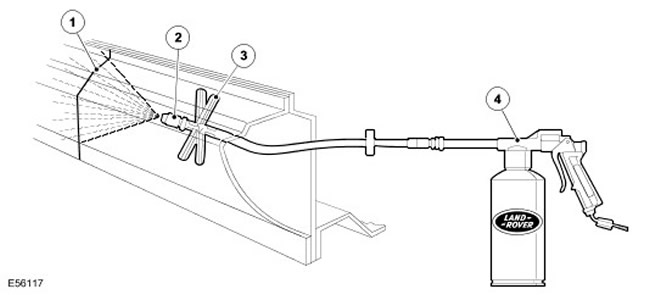
Item name | Spare part number | Description |
1 | - | Weld bead |
2 | - | spray head |
3 | - | spacer element |
4 | - | Spray |
Classification of various corrosion protection measures for dent removal
Corrosion protection method | External surfaces | Available interior surfaces | Inaccessible interior surfaces |
Coloring | X | X | |
Cavity Protection | X |
Classification of various corrosion protection measures when installing new parts
Corrosion protection method | Weldable flanges before welding in the required position (contact surfaces) | All deburred areas | Accessible area of welded flange | Inaccessible area of the welded flange |
Welding primer | X | |||
Coloring | X | X | ||
Curved edge protection | X | |||
Cavity Protection | X |
Body sealing materials
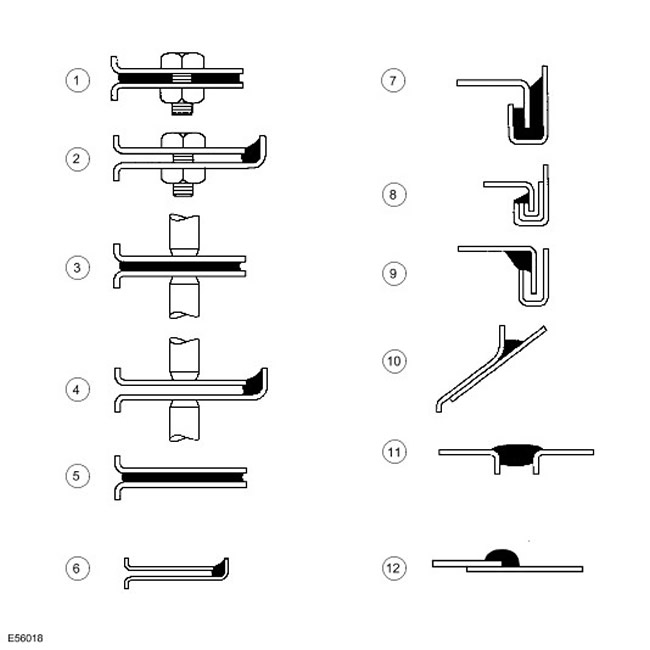
Item name | Spare part number | Description |
1 | Between panels - bolted connection | |
2 | Between the edges of the panels - bolted connection | |
3 | Between panels - spot welding connection | |
4 | Between the edges of the panels - spot welding connection | |
5 | Between panels - adhesive connection | |
6 | Between the edges of the panels - adhesive connection | |
7 | Lock connection - type A | |
8 | Lock connection - type B | |
9 | Lock connection - type C | |
10 | Gaps between panels - type A | |
11 | Gaps between panels - type B | |
12 | Lap joint |
Description - Application | Provider | spare part no |
Wax sealants for filling cavities | - | - |
Cavity Sealant (amber color) | 3M | 0890/11/21 |
Cavity Sealant (transparent) | 3M | 08909/19/29 |
Wax sealant for closed cavities | Croda | PW57 |
Wax sealants / varnishes for the engine compartment | ||
Engine Compartment Wax and Astrolan Cosmetic Coating | Astors | DA3243/1 |
Sealant and varnish for engine compartment and cosmetic purposes | Croda | PW197 |
Cosmetic varnish for the engine compartment | Dinol | 4010 |
Various materials | - | - |
Aerosol Auto Adhesive (Trim) - adhesive mastic for decorative details | 3M | 08080 |
Repair Material for Elastic Parts - Rubber Modified Polypropylene Parts | 3M | 05900 |
Soundproofing foam (sika baffle 278) - block repair with expanding foam | Sika | Land Rover part number: AZL 500021. Ford part number: 6H22-11840-AA |
Elastic foam (vibration absorption) - between panels | Duramix | 4320 |
Aerosol Water Shedder Repair (to remove moisture) | Teroson | - |
Low temperature anti-corrosion coating (for magnesium alloys) | Land Rover | VEP 501 840 PMA |
Seam sealing materials | ||
Body seal - gaps between panels (type b) | 3M | 08568 |
Drip Check Clear - sealing joints on bolts, on spot welding, on glue, gaps between panels like (A) And (b), connections in lock type (With) | 3M | 08401 |
Drip Chek Heavy - Type Clearances (b) between panels, connections in lock type (With) | 3M | 08531 |
Polyurethane Seam Sealer is a polyurethane based sealant for bolted, spot welded, adhesive, gap type (a) And (b) between panels, connections in lock type (b) | 3M | 08684/89/94 |
Polyurethane Sealer (Sachet) - polyurethane-based sealant for bolted edge joints, lock-type joints (b) | 3M | 08703/83/88 |
Aerosol Sealant - For Lap Joints | 3M | 08800/23 |
Super Seam Sealer - sealant for lap joints, lock type (b) | 3M | 08537 |
Weld Thru' Sealer - Penetrating Sealant for Spot Weld Joints | 3M | 08626 |
Betafill Clinch and Brushable Sealer - brushable sealant for lock type joints (b) | Gurit-Essex | 10211/15/20 |
Joints, seams and bottom sealing - lap joints | Gurit-Essex | 10101/10707 |
Leak Check Clear - sealing joints on bolted, spot welded, glued, gaps between panels like (A), connections in lock type (With) | Kent Industries | 10075 |
Putty is a sealant for filling gaps between panels like (b) | Kent Industries | - |
Polyurethane Seam Sealer is a polyurethane-based sealant for bolted, spot-welded, adhesive-bonded, glued-panel joints, panel-type gaps (A) And (b), connections in lock type (b) | PPG | 6500 |
Polyurethane Seam Sealer is a polyurethane-based sealant for bolted, spot-welded, glued, glued-panel joints, gaps between panels like (b) | Teroson | 92 |
Terolan Light Seam Sealer - sealant for bolted, spot welded, glued, gaps between panels like (A) And (b), between glued panels, lock type connections (c) | Teroson | - |
Terolan Special Brushable Seam Sealer is a brush applied sealant for overlapped seams. | Teroson | - |
Terostat Sprayable Seam Sealer is an aerosol sealant for bolted, spot welded, glued, glued panel joints, gaps between panels like (b) | Teroson | 9320 |
Terostat 1K PU Seam Sealer (SE 20) - gaps between panels (A) And (b), spot welding and glued panel edges. | Teroson | - |
Sealing Compound - sealant for bolted, spot welded, glued joints, joints between glued panels, gaps between panels such as (b) | Wurths | 8901001/-/6 |
Adhesive materials for body frame (structural) | ||
Automotive Structural Adhesive - for sealing joints on glue, joints in a lock type (A) | 3M | 08115 |
Two Part Structural Epoxy (two-component epoxy resin for carcass) - for joints on glue and spot welding, for joints in a lock type (A) | Ciba-Geigy | XB5 106/7 |
Underbody sealing materials | ||
Body-Schutz | 3M | 08861 |
Spray-Schutz | 3M | 08877 |
Crodapol Brushable Underbody sealer (bottom sealant) | Croda | PV75 |
Terotex Underseal (CP02) (for bottom) | Teroson | 9320 |
Wax mastics for the underbody | ||
Anti-gravel coating (smooth) | 3M | 08158/9 |
Underbody mastic | Croda | PW61 |
Underbody mastic | Dinol | Tectacote 205 |
Penetrating primers for welds | ||
Weld Thru' Coating (penetrating coatings for welds) | 3M | 05913 |
Zinc Spray (spray zinc primer) | 3M | 09113 |
Zinc Rich Primer (zinc primer) | ICI | p-565 634 |
Material Application Equipment/Suppliers
3M
- Automotive Trade Group
- 3M UK Pic
- 3M House
- PO Box 1
- Market Place
- Bracknell
- Berks
- RG12 1JU
- Telephone (01344) 858611
- Burgess Hill
- Sussex
- RH 15 9LA
- Telephone (014446) 42526
- Minden Industrial equipment
- 16 Greyfriars Road
- Moreton Hall
- Bury St Edmunds
- Suffolk
- IP32 7DX
- Telephone (01284) 760791
- Watchmead
- Welwyn Garden City
- Hertfordshire
- AL7 1JB
- Phone 01707 358800
Underbody sealing materials
The surface of the bottom and the outer panels of the thresholds are treated with Plastisol PVC bottom sealant. This material is not suitable for reprocessing. When repairing areas of the bottom with a broken sealant layer, clean the factory coating of the bottom in the damaged area to the metal. Make sure that the area to be treated is metallically clean and that the edges of the remaining layer of coating sealant adhere securely to the panel surface.
Apply a new coat of underbody sealant after applying the primer coat but before applying the paint. Apply weld sealant before applying bottom sealant. Ensure that all plugs and grommets in the floor panel (except for the plugs of the holes through which the sealant is applied) put in place before underbody sealant is applied. Use a heat gun to reinstall any hot melt plugs damaged during repair, or replace them with rubber bushings.
CAUTION: Before applying new sealant to the underside of the vehicle, cover all suspension components, wheels, tires, power pack, drive shafts, exhaust pipe, and brakes (including all attachment points).
Sealing area on the bottom of the car

Body Repair Precautions
Be careful when carrying out repair work in the workshop. Sealing and wax protective underbody coatings, weld seals, body panels can be damaged as a result of careless lifting of the vehicle.
Independent anti-corrosion treatment
It is not recommended to carry out anti-corrosion treatment yourself, in addition to factory treatment, as this may void the warranty on the anti-corrosion protection of the car. This does not apply to approved protective waxes that are compatible with and can be applied over existing coatings.
Approved accessory settings
When installing accessories, make sure that the vehicle's corrosion protection is not compromised by either damage to the protective layer or the formation of moisture-trapping areas.
Do not drive self-tapping screws directly into body panels. To do this, first install the correct plastic inserts. When drilling holes in panels, chassis members and other bodywork, always prime the edges of the holes with a suitable zinc or acid primer and then apply protective wax mastic around the hole with a brush.
Do not mount accessories with painted metal surfaces directly on body panels without prior protective treatment. When connecting metal surfaces to each other with bolts, always treat the joint planes with a weldable zinc primer, place zinc tape or protective material between the surfaces.
Steam cleaning
Due to the high temperature and pressure of steam cleaning, some adhesives and anti-corrosion materials may soften or melt.
Do not direct the steam jet at one place for too long and place the nozzle of the equipment no closer than 300 mm from the surface of the body.
ATTENTION: Do not remove the protective wax or paint coating from the surface of the bottom during repair work.
Maintenance check
A prerequisite for the effective operation of the factory anti-corrosion coating of the body is to check its condition by an authorized Land Rover dealer, at least once a year.
Repair body damage and corrosion detected during inspection as early as possible to minimize damage and ensure the effectiveness and long life of the factory anti-corrosion coating.
Bottom protective coating repair
In any case, when performing body repairs, ensure the complete restoration of the sealing and anti-corrosion coating. This applies both to damaged areas and to areas where the pavement has been disturbed, for example by accident or during repairs.
Before straightening or straightening the deformed area, remove the anti-corrosion coating from the damaged areas. This applies primarily to panels with a protective wax coating, PVC-based sealant for the bottom, sound-absorbing linings, etc.
CAUTION: Do not use an oxy-acetylene torch to remove the anti-corrosion coating. When these coating materials burn, large amounts of gases and smoke are released.
The most common way to remove sealant is to use a heat gun with a scraper. The high temperatures generated by this equipment may cause smoke to be emitted. Therefore, care must be taken.
Structural adhesive
Glue for metal is applied to areas of critical seams during the factory assembly of the body. In this case, the material used is a high-temperature thermosetting compound based on acrylonitrile and phenol-formaldehyde resin. The material sticks together two metal surfaces, being at the same time a sealant that protects against the penetration of dirt, moisture and gases into the joint. This material is not intended for use in body repair, so an approved structural adhesive for structural body members should be used instead.
ATTENTION: When separating parts joined together with metal glue, it is important not to deform the junction. Gradually heat up the joint until the adhesive has softened enough to allow the glued panels to be easily pulled apart.
NOTE: If spot welding is performed at the junction of parts joined with metal adhesive, the process parameters must be carefully selected to obtain a reliable weld.
Structural adhesive areas
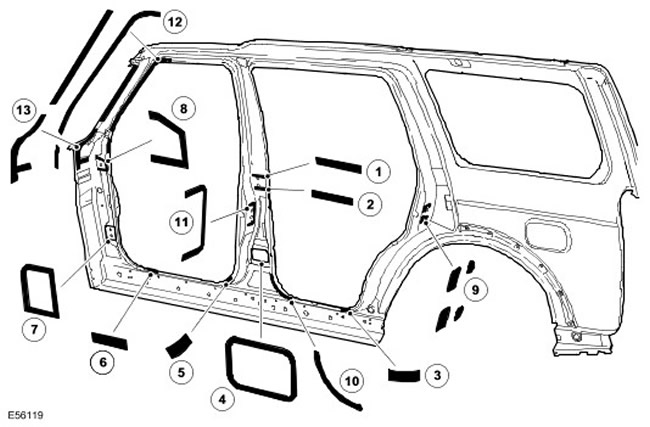
Name | Usage | Operating principle |
1 | Upper hinge of the right and left middle pillars of the body | Structural adhesive |
2 | Upper hinge of the right and left middle pillars of the body | Structural adhesive |
3 | Right and left rear door sill panels | Structural adhesive |
4 | Right and left rear door sill panels | Structural adhesive |
5 | Right and left front door sill panels | Structural adhesive |
6 | Right and left front door sill panels | Structural adhesive |
7 | Lower hinge of the right and left front pillars of the body | Structural adhesive |
8 | Upper hinge of the right and left A-pillars | Structural adhesive |
9 | C-pillar lock reinforcement | Structural adhesive |
10 | Gap between rear door and B-pillar | Structural adhesive |
11 | Latch surface on B-pillar | Structural adhesive |
12 | Gap between front door and A-pillar | Structural adhesive |
13 | Gap between waterproofing and A-pillar | Structural adhesive |
Welding seams located symmetrically as shown in the figure are also subject to processing. Apply a 3 mm bead of compound to all marked panel joints. Do not cover the sill drain holes with glue.
Soundproofing with foam
Expandable foam soundproofing seals are used in various enclosed body cavities to improve vehicle performance. These seals are applied during the manufacturing process of the vehicle and expand during body painting to approximately 10 times their volume, thus locking into place. Soundproof seals are placed in such a way that they make it difficult for sound to penetrate into the passenger compartment through the structural elements and through the air.
Depending on the location, these seals can have a dual purpose. Seals located at the base of the body pillars are mainly designed to isolate the body from water when overcoming water obstacles. Auxiliary purpose of these seals is sound insulation, and protection against dust penetration.
The main purpose of the seal around the fuel filler neck is to protect against the ingress of fuel and water. The auxiliary purpose of this seal is sound insulation, and protection against dust ingress.
The main purpose of the remaining seals is to prevent sound transmission to the passenger compartment through structural elements and through the air.
Another advantage of using sealing materials is a significant increase in the rigidity and strength of the body elements, which increases safety in the event of a collision.
These seals are made using 'Sika Baffle 250.'
Replacing foamed soundproofing seals
Since the annealing temperature of parts during painting during repair operations is much lower than during factory painting, a different technology is required when replacing seals during repair.
Following a repair involving the replacement of a structural element containing foam soundproofing, an approved foaming soundproofing sealant is introduced into the new element. Foaming soundproofing sealant is introduced after completion of painting work (where possible). When applying a foaming material, it must fill the entire space of the cavity.
Location of soundproofing, front reinforcement
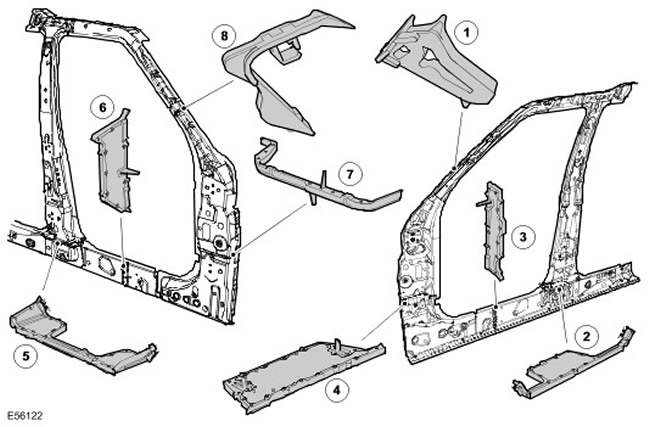
Name | Description | Operating principle | Part number according to the repair catalog |
1 | Upper inner panel of the A-pillar | Soundproofing | EUH000520 |
2 | B-pillar lower inner panel | Waterproofing / soundproofing | EUH000560 |
3 | Middle sill panel | Soundproofing | EUH000670 |
4 | Lower inner panel of the A-pillar | Waterproofing / soundproofing | EUH000550 |
5 | B-pillar lower outer panel | Waterproofing / soundproofing | EUH000570 |
6 | Exterior sill panel | Soundproofing | EUH000680 |
7 | Lower inner panel of the A-pillar | Waterproofing / soundproofing | EUH000540 |
8 | Upper outer panel of the A-pillar | Soundproofing | EUH000530 |
Sound insulation position, rear side panel
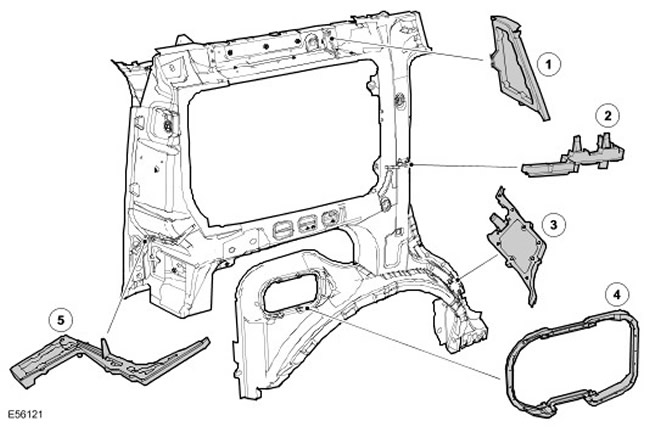
Name | Description | Operating principle | Part number according to the repair catalog |
1 | Rear top belt | Soundproofing | EUH000650 |
2 | C-pillar outer panel | Soundproofing | EUH000610 |
3 | Rear wheel arch outer panel | Waterproofing / soundproofing | EUH000590 |
4 | Opening for fuel filter | Waterproofing / protection against ingress of fuel | ARY 780030 |
5 | Rear door pillar outer panel | Soundproofing | EUH000630 |
Sealant for welds
At the factory assembly of the body, a heat-curing PVC-based sealing coating is applied to some of the panel joints. This material is not intended for use in body repair and must be replaced with an approved panel joint sealant.
The joint sealant is applied over the primer, but before the topcoat is applied.
The joint sealant should form a continuous bead, the profile of which depends on the type of joint. If the sealant material is applied with a brush, make sure to treat the entire surface of the joint.
Check that all accessible welds are sealed after repair. In a car collision, parts of the body located at a distance from the impact site are often deformed. As a result, the sealing coating in these areas may be damaged during the subsequent straightening of the panels and during repairs. Inspect all welds near the parts to be repaired for damage to the coating, then remove the damaged or cracked coating and apply a fresh coating according to the following procedure:
- Sand the area of the damaged coating down to metal and etch the cleaned surface with an appropriate phosphate primer.
- Treat the damaged surface with an acid primer.
- Apply proper joint sealant.
- Apply proper color coat (and sealant on the bottom, if applicable).
Seam sealer on the back
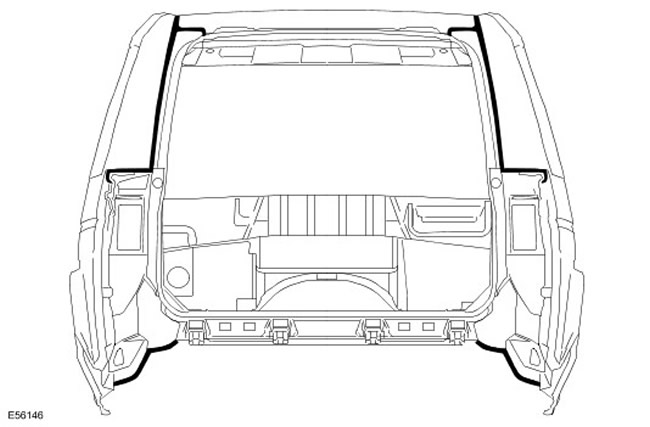
Bottom seam sealer
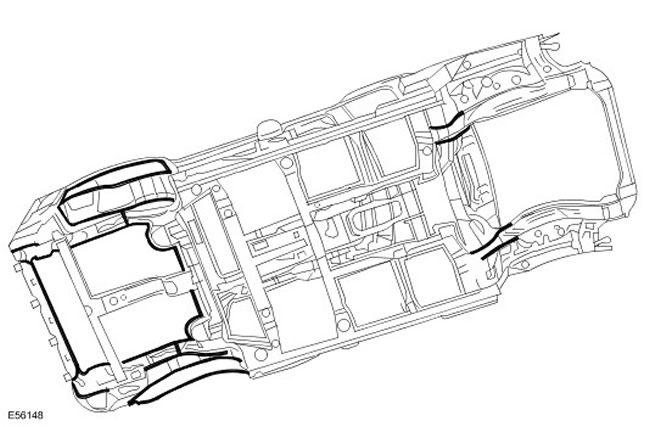
Wax sealant for closed cavities
Be sure to treat these areas with the proper cavity wax after repairs have been made. In addition, cavities that have been damaged during repair should also be treated, regardless of whether they were factory treated or not. This includes all box-shaped assemblies, cavities and interior door panels.
Before injecting a protective compound, make sure that the cavities to be treated are free of dirt and foreign matter. If necessary, clean the cavities of foreign particles.
The protective composition should be applied after painting is completed and before installing any decorative and overhead elements.
During processing, make sure that the protective compound covers all flanges and joints and that it is applied to all repaired places, both old and newly installed panels.
It should be noted that new panels and body assemblies are supplied with internal cavities already treated with a protective compound. Reprocess these cavities after repair.
Reliable processing of cavities is very important. Always observe the following rules:
- Finish all painting operations before applying the protective wax.
- Check the spray cone shape of the cavity treatment equipment.
- Cover all areas that cannot be treated with a protective coating
- If there is a risk of contamination from the protective coating, remove items such as seat belt pretensioners.
- before processing the internal cavities of the doors, completely close the windows.
- Treat areas of the body that are usually covered by overlays before installing these elements.
- After treatment with a protective compound, clean the drainage holes of the thresholds and doors.
- Keep all equipment clean, especially protective coating sprayers.
Protective wax areas, bodywork
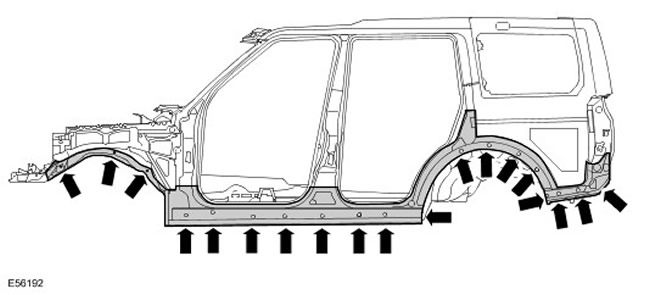
Protective wax areas, doors
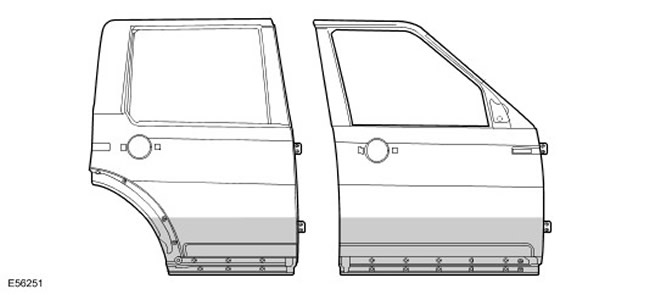
Comments on this article