Introduction
In the process of releasing new models, which replace each other faster and faster, the body plays a significant role. Different groups of customers are attracted, first of all, by the design and shape of the body. At the same time, the strength of the body plays the most important role in ensuring the safety of the driver and passengers. Modern Land Rover vehicle bodies are characterized by the use of alternative materials: composite materials and plastics combined with sophisticated bonding technologies.
Modern factory technologies make it possible to produce bodies with safety cages with virtually no problems (load-bearing bodies). To ensure a high level of quality, mechanical strength tests of materials are carried out, numerous computer simulations, collision tests of the body, advanced materials production technologies are applied. All repairs must be carried out in accordance with factory quality standards. This requires equipping technical centers with modern equipment and imposes special requirements on the qualifications of technical personnel. To ensure high-quality body repair, knowledge of the factory technologies used and constant training in new repair methods and technologies is essential. Model-specific repair manuals and general repair procedures provide invaluable assistance when performing body repairs.
Strictly follow the repair technology described in this manual. Failure to comply with the repair technology can lead to a serious decrease in the level of vehicle safety. After carrying out the repair work, it is necessary to ensure that all the prescribed safety standards are observed.
Vehicle design
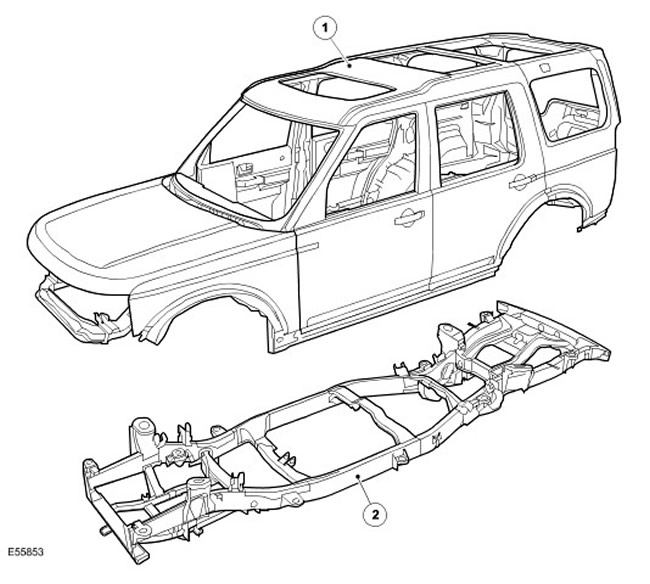
Item name | Spare part number | Description |
1 | body type | |
2 | body frame |
High strength steel grades
Most modern cars are made using steels of various grades, which allows you to optimize the body structure (collision, safety, rigidity, reduced fuel consumption, etc.).
Steels are divided into several groups according to tensile strength and yield strength (force that leads to plastic deformation of the material).
Yield strength
The yield point is the force at which the metal loses its elasticity and begins to plastically deform without subsequent restoration of shape.
Tensile strength
The tensile strength is the force at which the tensile specimen breaks.
Abbreviation | steel grade | Yield strength |
SS | Soft (low carbon) steel | Yield strength no more than 220 MPa |
DP | Duplex steel | Steel with yield strength up to 400 MPa |
HS | high strength steel | Steel with a yield strength of 220 -450 MPa |
EHS | Heavy duty steel | Tsstal with a yield strength of 450 -800 MPa |
UHS | Ultra strong steel | Steel with yield strength up to 1400 MPa |
Ultra high strength
Ultra-strength steel elements, which are used in the A-pillars, B-pillars and upper belt, increase the body's resistance to deformation in frontal or side impacts.
Ultra high strength steel elements cannot be straightened due to their brittleness.
The use of ultra-strong steel in the body structure

Aluminum
The hood, tailgate and tailgate are made from 6000 aluminum, an aluminum-magnesium-copper alloy that is heat-treated during manufacturing to increase the panel's strength and dent resistance.
When repairing aluminum parts, a separate set of tools should be used, which should not be used when working on steel parts - this will avoid cross-contamination of metals.
The use of aluminum in the body structure
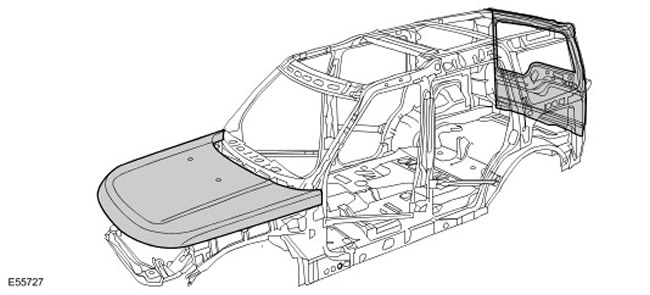
Magnesium
AM60B magnesium alloy is used to make the hood latch panel. It has a high viscosity and absorbs impact energy well. This alloy is also used to make the cross member on which the instrument panel is mounted.
It is not allowed to straighten the hood latch panel or carry out welding work on it - in case of an accident, the panel replaces the assembly. If the anti-corrosion coating is damaged, it must be repaired using 'Land Rover Low Temperature Anti-Corrosion Coating', part number VEP 501 840 PMA.
The use of magnesium in body structure
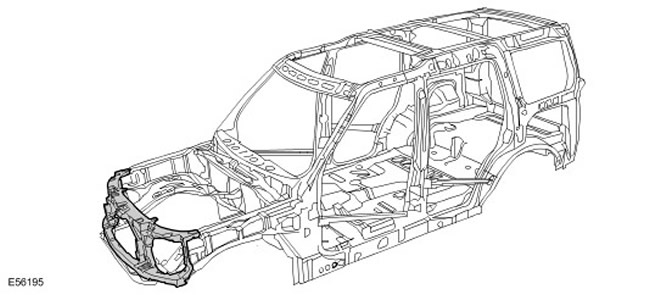
Crash Damage and Diagnostics
General Notes:
- Accurate diagnosis of damage severity ensures proper repair planning.
- All types of body repairs must be carried out in strict accordance with the instructions in the Body Repair Manual.
- When carrying out body repairs, the stability and strength characteristics of the body must be taken into account. The body structure is designed for specific deformation patterns that are not allowed to be changed during repair work.
- For example, crumple zones absorb a large proportion of the impact energy in a collision. If any non-professional methods or techniques are used to repair these areas, the safety of the vehicle may be affected.
- In addition to checking for external signs such as peeling paint, be sure to check for hidden damage or deformation of the bodywork that is not visible from the outside. To accurately assess damage to hidden body parts, it is often necessary to remove large attachments such as bumpers and inner fenders.
Another diagnostic option through visual inspection is to check the dimensions of the gaps. Any changes or violation of the mutual position of the edges usually indicate a change in the size of the damaged parts.
Resizing gaps
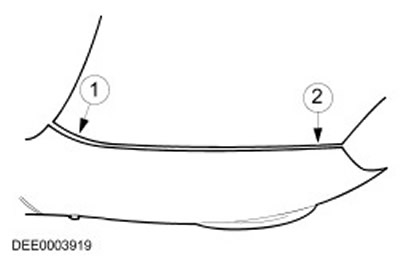
Item name | Spare part number | Description |
1 | Too much gap | |
2 | Too little clearance |
Repair planning
Before starting repairs, the following decisions must be made:
- Does the car need to be installed on a slipway or can it be straightened in another way?
- Is it necessary to carry out control measurements of the body?
- Is it necessary to remove components such as the engine or axles?
- What body parts need to be replaced?
- What parts of the body can be repaired?
NOTE: It is preferable to repair body parts rather than replace them as this will preserve the integrity of the body.
Getting spare parts
The availability of spare parts often determines how easily a body repair can be completed. The following procedure is recommended:
- Get all vehicle details including type, vehicle identification number, trim code, engine letter ID, original registration data, and more.
- Identify all metal parts that need to be replaced.
- Identify all attachments that need to be replaced, including small parts such as rivets, clips, etc.
Repair with editing
Straightening repairs are often required to restore the original body shape after a collision. This can be done using:
- Alignment stands
- Universal stand for straightening and measuring
Structure: The repair sequence depends on the individual repair plan (including all necessary disassembly work). Clean the connection areas. Fix the car on the appropriate stand in such a way that it does not create tension in it. Place the units on supports to relieve the load from the body. Select at least three measuring/fixing points that are not damaged and located as far apart as possible (for basic adjustment). Check the dimensions at the measurement/fixing points.
- The repair sequence depends on the individual repair plan (including all necessary disassembly work).
- Clean the connection areas.
- Fix the car on the appropriate stand in such a way that it does not create tension in it.
- Place the units on supports to relieve the load from the body.
- Select at least three measuring/fixing points that are not damaged and located as far apart as possible (for basic adjustment).
- Check the dimensions at the measurement/fixing points.
Editing: NOTE: During the editing process, constantly check the dimensions and clearances.
Body dressing is always done in the opposite direction to the impact. Always make adjustments with the body fully assembled (do not pre-cut any elements). Carry out editing in several stages. This eliminates the risk of overstretching panels or tearing welds. At each individual step of dressing, aim to release tension from parts subject to tensile load with blows of an aluminum hammer (previously identified deformations, dents, welds, etc.)
NOTE: During dressing, constantly check the dimensions and clearances.
Body dressing is always done in the opposite direction to the impact. Always make adjustments with the body fully assembled (do not pre-cut any elements). Carry out editing in several stages. This eliminates the risk of overstretching panels or tearing welds. At each individual step of dressing, aim to release tension from parts subject to tensile load with blows of an aluminum hammer (previously identified deformations, dents, welds, etc.)
WARNING: Ultra-strong steel elements used in the A-pillar, B-pillar and upper belt cannot be straightened.
Straightening
Basic principles of straightening panels:
- Before replacing any sections or completely replacing body panels, always check carefully to see if the damaged panel can be straightened out.
- Straightening is usually the easiest and most economical method of repairing a damaged panel.
- Aluminum hammer and mallet Advantage: low chance of panel overstretching. Used to repair small dents in panels that are accessible from both sides. These two panel straightening tools are commonly used for "finishing" repair operations.
- Benefit: Low chance of overstretching the panel.
- Used to repair small dents in panels that are accessible from both sides.
- These two panel straightening tools are commonly used for "finishing" repair operations.
"Thin" straightening with an aluminum hammer and a universal backing die
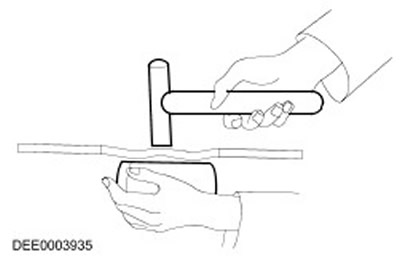
Moving hammer If the damaged panel is only accessible from the outside, use a moving hammer to reshape the panel. The discs or studs needed to mount a moving hammer are welded to a surface that has been cleaned to metal. Dents in the panel can be corrected with the controlled application of a moving hammer.
- If the damaged panel is only accessible from the outside, use a moving hammer to reshape the panel. The discs or studs needed to mount a moving hammer are welded to a surface that has been cleaned to metal. Dents in the panel can be corrected with the controlled application of a moving hammer.
Cutting body parts
Depending on the elements to be installed, different tools must be used to cut or separate body parts.
NOTE: All other components such as trim, window glass, etc. must be protected from flying sparks.
NOTE: Be sure to set the depth of cut correctly to avoid loosening the rest of the flange.
Milling of spot welds
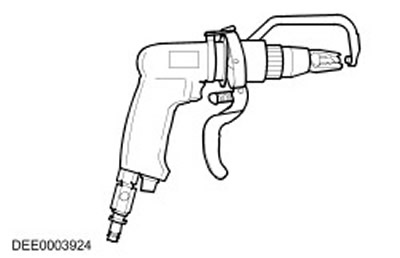
- Face grinding wheel
NOTE: Use protective clothing. Protect all vulnerable parts of the bodywork or glass from flying sparks. Remove explosive materials from work area.
Spot welds that cannot be removed by milling (diameter > 8 mm), should be selected using the end grinding wheel. The same applies to spot and conventional welds made using MIA technology.
NOTE: Use protective clothing. Protect all vulnerable parts of the bodywork or glass from flying sparks. Remove explosive materials from work area.
Spot welds that cannot be removed by milling (diameter > 8 mm), should be selected using the end grinding wheel. The same applies to spot and conventional welds made using MIA technology.
Face grinding wheel
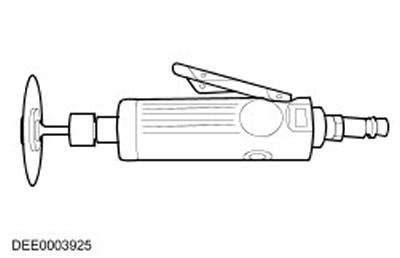
NOTE: Be careful not to damage metal components, wiring harnesses, hoses, etc. located under the part being cut out, if necessary, remove them beforehand.
Bodywork saws are versatile and therefore well suited for cutting body parts.
Short stroke saw
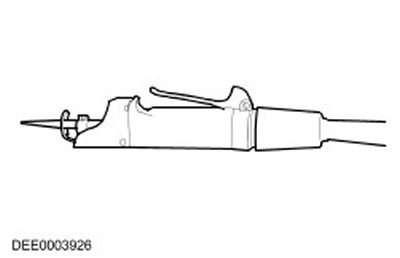
Reciprocating Saw In addition to the short stroke saw, you can also use a reciprocating saw. It allows you to make narrow and straight cuts to a precisely defined depth.
In addition to a short stroke saw, a reciprocating saw can also be used. It allows you to make narrow and straight cuts to a precisely defined depth.
Reciprocating Saw
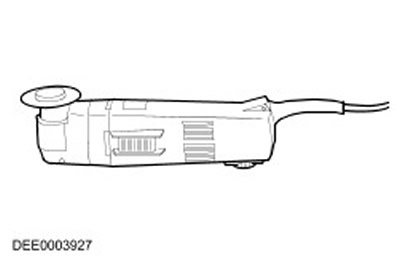
Carrying out repairs
Complete replacement In a complete replacement, the entire damaged "old" the element is separated at its junctions and then a new element is installed in its entirety. The picture below shows the new replacement rear body panel.
With a complete replacement, the entire damaged "old" the element is separated at its junctions and then a new element is installed in its entirety. The picture below shows the new replacement rear body panel.
Rear Panel Replacement
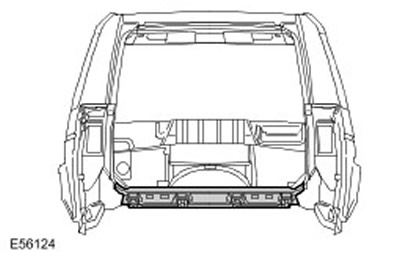
Partial replacement It is often technically and economically advantageous to carry out a partial replacement. The two main criteria are, firstly, the preservation of the original body structure, and, secondly, the reduction of repair costs to a minimum.
Often, from a technical and economic point of view, it is advisable to carry out a partial replacement. The two main criteria are, firstly, the preservation of the original body structure, and, secondly, the reduction of repair costs to a minimum.
Basic Partial Replacement Technique: Butt Joints New and old parts are joined by a continuous MIG weld. Butt joints are typically used when partially replacing frame members and studs or other members with short cut lengths.
- Butt joints.
- The new and old parts are joined by a continuous MIG weld.
- Butt joints are commonly used when partially replacing frame members and studs or other members with short cut lengths.
Butt joint
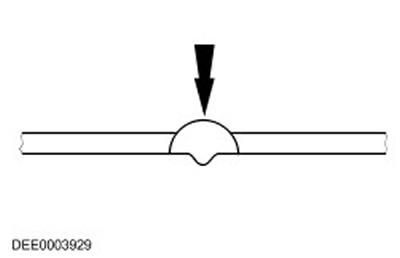
NOTE: Partial replacement cuts should be as short as possible. Cutting can only be done along the cut lines shown in the repair diagrams. It is forbidden to make cuts near reinforcements or along predetermined fold lines.
Prepare parts left on the vehicle and new parts. Using a hammer and mandrel, restore the original shape of all mating surfaces on the deformed body parts left on the car (make sure the shapes match "old" and new details to each other). Sand off any remaining spot or regular welds using the appropriate tool. Cut out new pieces to shape. If necessary, punch or drill holes for MIG welding.
NOTE: Do not use welding torch to remove paint residue (heat can cause deformation of the metal).
Strip mating flanges to metal on both sides. Do not use an angle grinder for this purpose (this can weaken the metal and damage the zinc layer). Required tools: Rotating wire brush, belt sander or plastic disc. Apply a sufficient amount of welding primer to the surfaces to be welded. Stir the primer thoroughly before use.
- Using a hammer and mandrel, restore the original shape of all mating surfaces on the deformed body parts left on the car (make sure the shapes match "old" and new details to each other). Sand off any remaining spot or regular welds using the appropriate tool.
- Cut out new pieces to shape.
- If necessary, punch or drill holes for MIG welding.
- Strip mating flanges to metal on both sides. Do not use an angle grinder for this purpose (this can weaken the metal and damage the zinc layer). Required tools: Rotating wire brush, belt sander or plastic disc.
- Apply a sufficient amount of welding primer to the surfaces to be welded.
- Stir the primer thoroughly before use.
NOTE: Do not use welding torch to remove paint residue (heat can cause deformation of the metal).
NOTE: When using aerosols, be careful not to contaminate adjacent areas.
Fixing a new part:
- It is necessary to accurately fit the new part to the specified dimensions. For this, it is recommended to use the following tools:
- Alignment stand
- Universal measuring system
- assembly stand
- Ruler or tape measure
- This stage installs all body attachments that require precise fit and installation, such as bumpers, seals, headlights, taillights, and lockout assembly components. Careless work can result in water leaks, wind noise intrusion and a significant amount of extra work.
- Check the alignment of the edges of the mating parts and check the equality of the gaps (compare left and right sides). Make sure to keep the shape of the car.
NOTE: Additional work can be greatly reduced if alignment and tack welding operations are performed with due care.
- Depending on the situation, fastening can be carried out by the following methods:
- Clamps (set)
- Screw terminal (set)
- Self-tapping screws
- Tack welds
- Using the proper tools, align the edges of the replacement relief pieces. The edges are then tack welded to ensure proper alignment of the pieces.
Alignment and tack welding
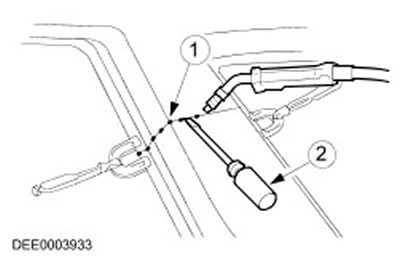
Item name | Spare part number | Description |
1 | Tack welds | |
2 | Align with proper tools |
- Longer connections are usually made with tack welds to prevent warping of the panel. It is important to perform tack welds in the correct sequence (see diagram).
- Weld the new part following the instructions in the repair manual.
Correct tack welding sequence
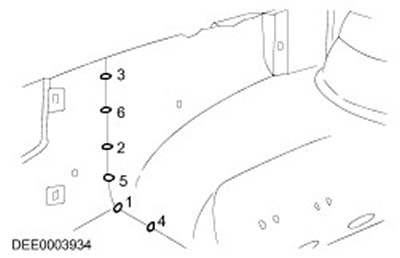
Precautionary measures
- Vehicle-mounted electronic control units (ECM) make it necessary to observe safety precautions when performing repair welding work. The intense heat and vibration associated with welding can damage electronic components. In particular, certain precautions must be observed when removing or disconnecting the SRS control unit (RCM) For more information refer to Specifications (501-20B)
- Do not allow electronic modules or busbars to come into contact with "weight" or power supply to the welding electrode.
- Connect the earth connection of the electric welding equipment directly to the element to be welded. Make sure there are no electrical insulators between the ground connection and the welding site.
Contact spot welding
Where resistance spot welding has been used in the construction of the bodywork, spot welding should also be used when replacing parts, if possible. In these new welding joints, the welding points should be 25 to 30 mm apart.
Equipment setup and selection of welding parameters:
- Hardware: Follow the hardware manufacturer's instructions to set up the hardware. Choose the right electrode holders (as short as possible). Accurately align the position of the electrode holders and tips. The tips of the electrodes must be convex (pre-shape with a file and finish it with a grinding tool).
- Follow the hardware manufacturer's instructions to set up the hardware.
- Choose the right electrode holders (as short as possible).
- Accurately align the position of the electrode holders and tips.
- The tips of the electrodes must be convex (pre-shape with a file and finish it with a grinding tool).
- Body: Make sure that the flanges to be joined match exactly. Clean the surfaces to be joined to metal (inside and outside).
- Make sure the flanges to be connected match exactly.
- Clean the surfaces to be joined to metal (inside and outside).
- Practice/Technology Notes: Make a test weld on a sample of material covered with welding paste. If any metal elements are located between the electrode holders, this will lead to a decrease in induction, and, consequently, to a loss of power (adjust current settings). For high- and ultra-strength steels, individual power settings should be selected. Re-welding over old welds results in poor quality welds. Hold the electrode tips at an angle to the contact surface as close to 90°as possible. Electrodes work best if they are convex. Regularly clean the contact surface of the electrodes.
- Make a test weld on a piece of material covered with welding paste.
- If any metal elements are located between the electrode holders, this will lead to a decrease in induction, and, consequently, to a loss of power (adjust current settings).
Welding equipment used to repair the bodies of modern Land Rover vehicles must ensure reliable welding of galvanized high-strength steel panels, consisting of three or more layers with a total thickness of up to 5 mm. If resistance welding equipment does not meet these requirements, electric rivet welding must be used for safety reasons. Electrical characteristics (current, resistance, heat) Spot welding equipment varies depending on the type of equipment. Therefore, to ensure the actual performance of the welding process, it is important to follow the equipment manufacturer's instructions.
MIG/MAG welding
Equipment setup and selection of welding parameters:
- Any joints made during the manufacture of the vehicle using MIG / MAG technology must be connected by welding using the same technology during the repair process. In addition, during the repair process, individual points of resistance welding should be replaced with cork welds.
- Partial replacement of resistance welding points with cork welds (see above) also produced with difficult access or lack of equipment for contact welding on thicknesses over 3 mm. But this leads to an increase in the time to complete the operation, and, accordingly, to an increase in the requirements for corrosion protection.
- Welding repairs can only be carried out properly if the equipment and all welding parameters are correctly set up.
- Equipment: Set up the equipment in accordance with the manufacturer's instructions. The hoses must not be twisted. The core must not be contaminated with abrasive particles. Gas nozzles must not be clogged with slag and scale. Pay attention to the quality of the electrode wire and the gas consumption.
- Set up the equipment in accordance with the manufacturer's instructions.
- The hoses must not be twisted.
- The core must not be contaminated with abrasive particles.
- Gas nozzles must not be clogged with slag and scale.
- Pay attention to the quality of the electrode wire and the gas consumption.
- Body: Make sure that the mating surfaces fit correctly. Clean the surface at the junction down to metal. Ensure correct clearances (seam root formation).
- Make sure the surfaces to be joined are properly aligned.
- Clean the surface at the junction down to metal.
- Ensure correct clearances (seam root formation).
- Notes on the methodology / technology:
- Connect the earth cable near the welding site (make sure the contact quality is good). When using a plug weld for high-quality penetration, you need to start welding from the bottom panel.
- Connect the earth cable near the welding site (make sure the contact quality is good).
- When using a plug weld for high-quality penetration, you need to start welding from the bottom panel.
NOTE: The increased heat in MIG welding destroys the weld primer/zinc over a larger area than resistance spot welding, resulting in increased labor costs for the subsequent application of an anti-corrosion coating.
NOTE: A test weld should always be made to ensure that the weld does not only connect to the surface.
NOTE: The increased heat in MIG welding destroys the weld primer/zinc over a larger area than resistance spot welding, resulting in increased labor costs for the subsequent application of an anti-corrosion coating.
NOTE: A test weld should always be made to ensure that the weld does not only connect to the surface.
Welding with electric rivets (cork weld)
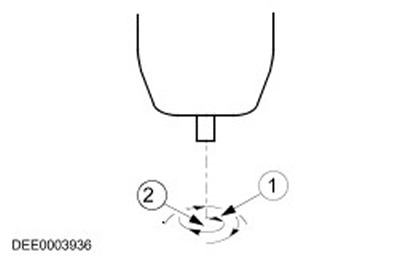
Item name | Spare part number | Description |
1 | Welding direction: circular motion, from inside to outside | |
2 | Weld start point: center of hole on bottom panel |
Adhesive glazing
- The windshield, side windows, and tailgate glass are fixed with adhesive directly to the body window frames and tailgate.
- Window panes are fixed in this way primarily due to the strength of the adhesive bond. Adhesive glazing gives the body additional torsional rigidity.
Adhesive glass installation
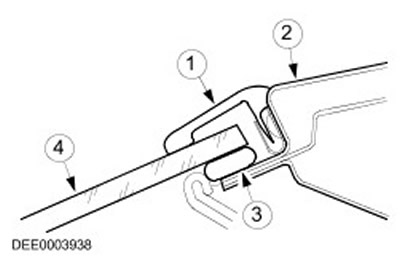
Item name | Spare part number | Description |
1 | Rubber strip | |
2 | window frame | |
3 | Glue | |
4 | window glass |
Removal and installation of windows with glued glass
Precautionary measures
To prevent injury, observe the following safety precautions:
- Use protective gloves.
- Use safety goggles.
- Before cutting a window with glued glass, loosen and remove all attachments located in the cutting area that are at risk, such as trim panels and decorative trims, as well as all electrical connections.
- Close all painted areas near the window.
- Trim off any excess glue as this makes it easier to cut the glass.
- Fix the glasses vertically to prevent them from falling out.
- Carry out cutting on the glue bead in easily accessible places using a cutting tool.
- Carefully guide the cutting tool along the perimeter of the window, cutting through the bead of glue.
- Do not touch the window frame and body flange.
- Use special "suction pads", to remove the glass from the window opening.
- Follow the manufacturer's instructions.
- Trim the remaining adhesive bead on the metal flange to a residual height of approx. 1 mm. After that, do not touch or clean the cutting surface.
- Carefully repair any damage to the paintwork (apply primer and top coat).
- Replace window stops if necessary.
- Apply an even bead of adhesive to the window or body flange.
- Insert the glass into the window opening and center it (2 mechanics required).
- Check gaps.
- Use adhesive tape to keep the glass from falling out.
NOTE: While the glue on the window is drying, open the windows and doors and do not move the car (slamming doors creates excess pressure that can loosen window fasteners).
Final operations:
- Connect all electrical connections and check the correct operation of the components.
- Install the attachments and check the accuracy and reliability of fastening. Perform a visual inspection to ensure that the gaps and joints are even.
- Perform a visual inspection to ensure that the gaps and joints are even.
- Completely clean the window glass.
Protective devices and work safety
When carrying out repairs, the safety and regulatory requirements must be observed. Compliance with all labor protection and safety regulations is mandatory.
Welding Precautions
- To prevent the risk of injury, observe the following precautions:
- Welder's mask (face protection)
- Protective shield
- Protective gloves
- Safety boots
- Welding fume extractor
- Welding should always be done in a well ventilated area. A fire extinguisher must always be within reach.
General safety rules for body repair
Sucking
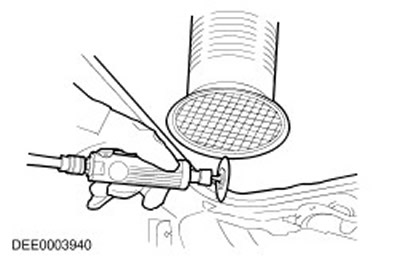
- Sealant, underbody protection, etc. should not be burned with an open flame. This results in the release of toxic gases. For example, when PVC is burned, gases containing hydrochloric acid are released. For this reason, when grinding, welding or soldering, always use the correct suction.
- Always ensure good ventilation when working with materials that contain solvents, use respiratory protection and suction equipment.
- Hearing protection should always be worn when cutting, grinding or straightening metal as noise level can reach or even exceed 85-90 dB (A).
- When removing parts from a car mounted on a lift, watch for changes in the position of its center of gravity. When placing the vehicle on a lift for the first time, please note that it may be necessary to secure it to prevent it from tipping over.
- When straightening, chains and chain clamps should be secured with safety cables.
Safety wire
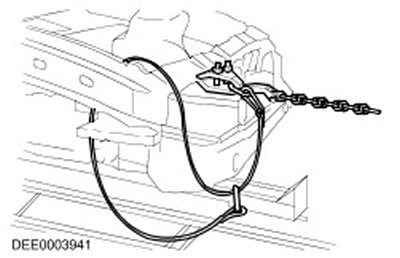
Preparing for painting
Thoroughly clean the vehicle with a steam cleaner or pressure washer before performing paint repairs.
Immediately before applying paint, wash repaired areas with a mild detergent solution in water and wipe clean with solvent.
Be sure to clean the damaged areas down to the metal, and the cleaned area should extend beyond the boundaries of the damaged area. Etch bare metal surfaces with a phosphate primer to remove any remaining rust and prepare the base for new coats of paint. Re-treat the damaged surface with either an acid primer and two-component putty alone or a combination acid primer/filler and apply a two-component paint coat. After applying paint, treat unpainted surfaces with an approved cavity wax.
CAUTION: When preparing to paint the bumpers, be careful not to damage the PDC sensors. If possible, remove only the clear coat. When painting PDC sensors, do not apply too much paint, as this may impair their performance.
WARNING: When using thermoset paint, the processing temperature must not exceed 65°C (149°F). Exceeding this temperature can warp the headlight and taillight reflectors and damage other components.
Comments on this article