Special tool (s)
![]() | Ladder Frame Adjustment Tool 303-1095 |
![]() | Pointer, top dead center (TDC) 303-1094 |
![]() | Crankshaft alignment tool 303-698 |
![]() | Tool for removing / installing the front crankshaft oil seal 303-679 |
![]() | Adjustment tool, engine front cover 303-682 |
![]() | Clutch Adjustment Tool 308-419 |
Assembly
1.
NOTE: The grooves in the crankshaft thrust washers must face up.
Install the crankshaft thrust rings. Lubricate the thrust rings with clean engine oil.
2. Install the crankshaft.
- Lubricate the crankshaft journals and crankshaft main bearing shells with clean engine oil.
- Install the crankshaft bearing shells.
3.
Caveats:
- Assemble the covers so that the arrows point forward. Covers are marked from the front in the following order: F, 2, 3, 4, R.
- Crankshaft main bearing cap bolts may only be used 4 times.
- Tighten the bolts in three steps in the sequence shown.
NOTE: Lubricate the crankshaft and crankshaft main bearing shells with clean engine oil.
NOTE: Use a center punch to mark the bolt heads for reuse.
Install the crankshaft main bearing caps.
- Stage 1: 45 Nm.
- Stage 2: 80 Nm.
- Stage 3: 105 degrees.
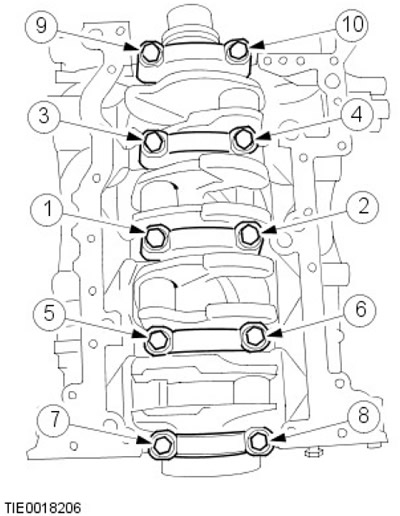
4.
CAUTION: Be careful not to damage the connecting rod bearing surface of the big end of the crankshaft connecting rod.
NOTE: Piston ring gaps must be evenly distributed around the piston circumference. This also applies to the elements of the oil scraper ring. Position the piston ring gaps at 120 degrees to each other.
NOTE: The arrow on the piston must point towards the front of the engine.
Using the appropriate tool, install the pistons. Lubricate the pistons and cylinder bores with clean engine oil.
5.
Caveats:
- Connecting rod bearing cap bolts may only be used 4 times.
- Check that the connecting rod bearing cap with profiled connector is correctly installed.
NOTE: Use a center punch to mark the bolt heads for reuse.
NOTE: The identification marks on the big end bearing caps must face the front of the engine.
Install the connecting rod bearing shells.
- Lubricate the connecting rod bearing shells with clean engine oil.
- Tighten the bolts in two steps.
- Stage 1: 30 Nm.
- Stage 2: 80 degrees.
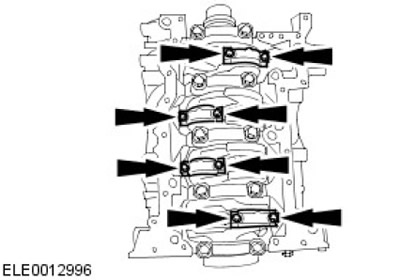
6.
CAUTION: Do not cut or damage the protruding foam pads.
NOTE: Install new step frame spacers.
Install the step frame. Screw in the bolts, but do not tighten them.
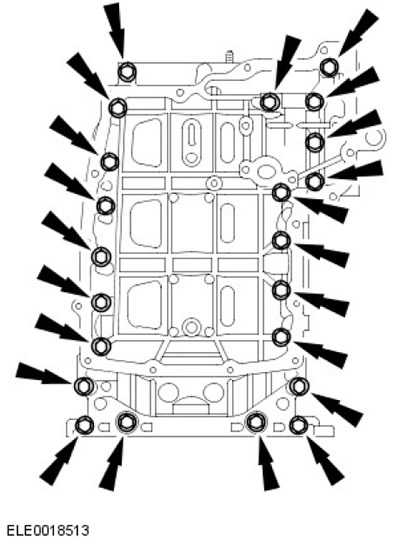
7.
CAUTION: The step frame and cylinder block must be aligned so that the side clearance does not exceed 0.05 mm to either side.
Using the special tool, align the position of the stepped frame with respect to the cylinder block.
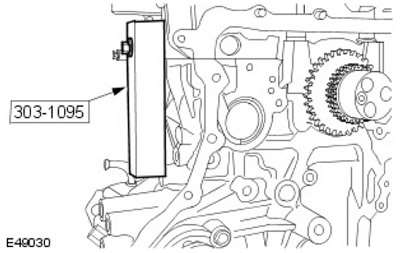
8.
CAUTION: The position of the stepped frame and cylinder block must be aligned so that the rear misalignment does not exceed 0.01 mm overlap / 0.2 mm gap.
Using a suitable straightedge, align the stepped frame with the cylinder block.
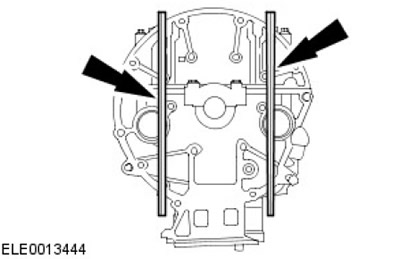
9.
NOTE: Tighten the bolts in the order shown in the illustration.
Attach the step frame. Tighten the bolts to 23 Nm.
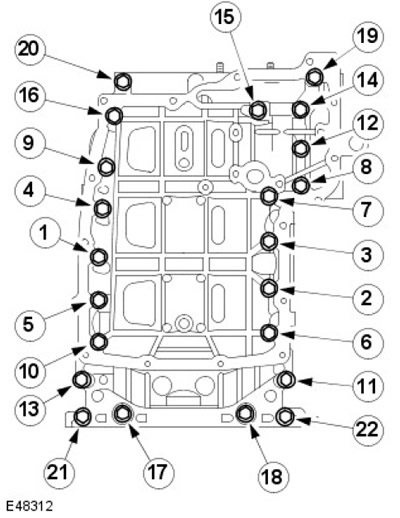
10.
NOTE: Install a new crankshaft rear oil seal.
NOTE: A new crankshaft rear oil seal has a locating sleeve that must be removed after installation.
NOTE: Tighten the bolts in the order shown in the illustration.
Install the crankshaft rear oil seal. Tighten the bolts (tightening torque 10 Nm).
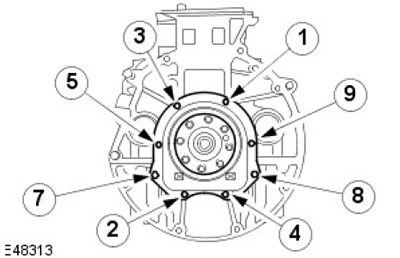
11. Remove special tools. Turn out a bolt.
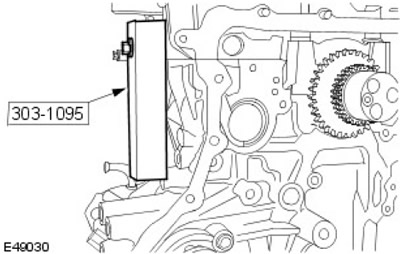
12.
NOTE: Do not fully tighten the fuel pump bolts at this stage.
Install the oil pump and oil pump chain. Slide the oil pump chain onto the crankshaft sprocket.
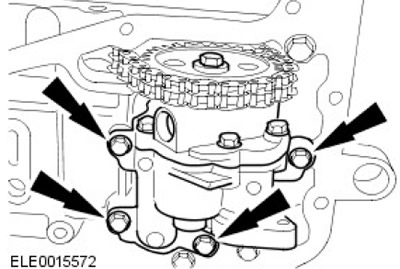
13. Using a suitable dial indicator, take a control measurement from the front of the crankshaft sprocket.
- 1. Place the dial indicator stand on the cylinder block.
- 2. Move the dial indicator plunger to the crankshaft sprocket and set the indicator to zero.
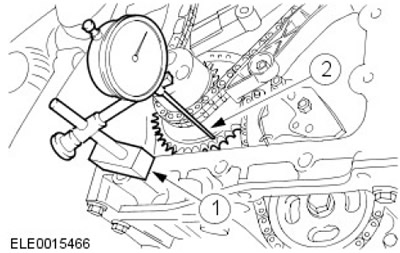
14.
NOTE: Take measurements at two different points on the oil pump sprocket.
Using a dial indicator, align the oil pump sprocket and tighten the oil pump mounting bolts.
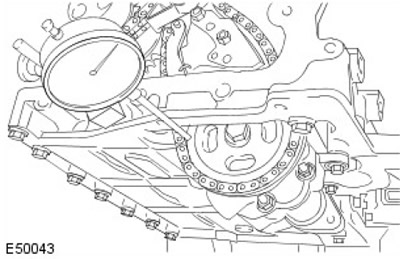
15. Check the alignment of the oil pump sprocket with the crankshaft sprocket. If necessary, repeat the alignment procedure.
16. Fix the oil pump. Tighten the bolts (tightening torque 10 Nm).
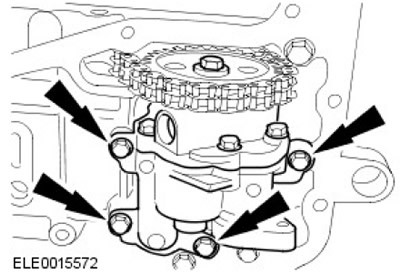
17. Install the oil pump chain tensioner.
- 1. Install the spring on the stud.
- 2. Unlock the tensioner by removing the pin.
- 3. Tighten the bolt (tightening torque 22 Nm).
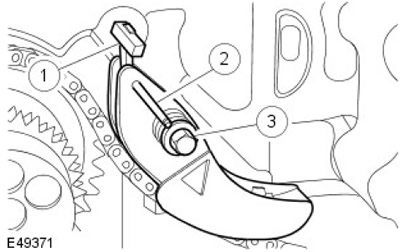
18.
NOTE: Install the o-ring.
Install the oil pump intake pipe. Tighten the bolts (tightening torque 10 Nm).
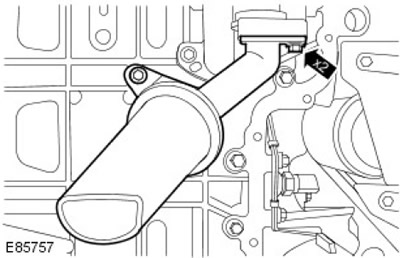
19.
NOTE: Tighten the bolts in two steps in the sequence shown.
Install a new oil sump.
- Apply a 3mm wide bead of recommended sealant to the oil sump.
- Stage 1: Tighten bolts 1 to 16 to 7 Nm.
- Stage 2: Tighten bolts 1 to 16 to 14 Nm.
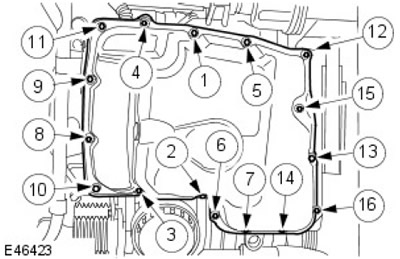
20.
NOTE: Install new flywheel bolts.
NOTE: Tighten bolts in three stages, working in sequence.
Install the flywheel.
- Stage 1: 25 Nm.
- Stage 2: 40 Nm.
- Stage 3: 48 degrees.
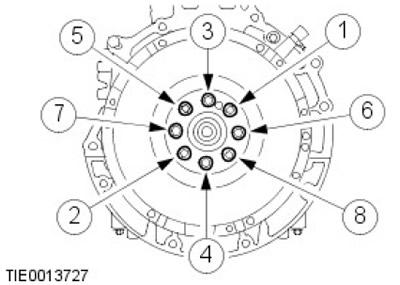
21.
NOTE: Tighten the bolts in the order shown in the illustration.
Using the special tool, install the clutch disc and pressure plate. Tighten the bolts (tightening torque 29 Nm).
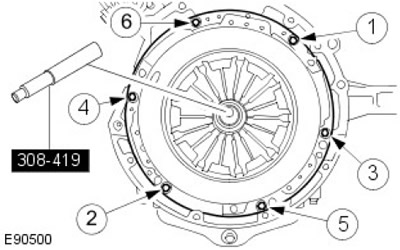
22.
NOTE: Do not fully tighten the crankshaft position sensor bracket bolts at this point.
Install crankshaft position sensor bracket (CKP).
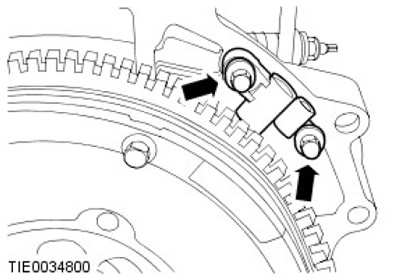
23.
NOTE: Do not move the special tool after installation.
Install the special tool.
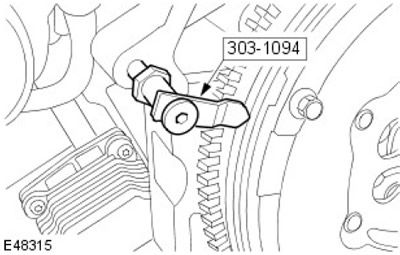
24. Rotate the crankshaft so that the No. 1 piston is approximately 10 mm from top dead center (TDC).
25. Establish the digital indicator on the block of cylinders.
- Install the digital indicator plunger on the #1 piston.
- Set the dial indicator to zero.
26. Mark the position on the flywheel.
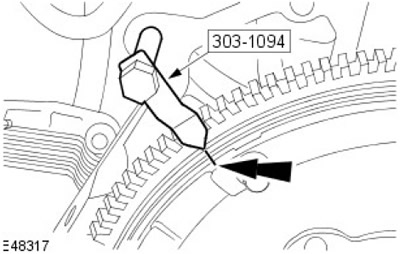
27.
NOTE: Rotate the crankshaft counterclockwise.
Rotate the crankshaft until the #1 piston is at zero on the dial indicator. Mark the position on the flywheel.
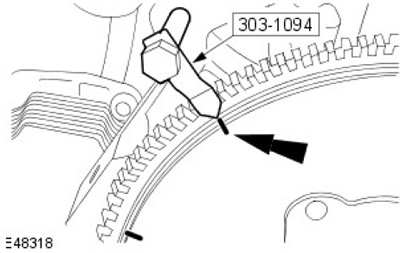
28. Repeat the previous steps to make sure the marks are correct.
29.
NOTE: The middle position between the marks is top dead center (TDC).
Measure the distance between the two marks.

30. Divide the value by two and note the TDC position on the primary section of the flywheel.
31. Measure the circumference of the flywheel.
32.
NOTE: Mark the calculated value on the primary section of the flywheel counterclockwise from TDC.
Multiply the circumference by 0.1388.
- 1. First label.
- 2. Second label.
- 3. Estimated position of TDC.
- 4. Estimated position 50 degrees before TDC.
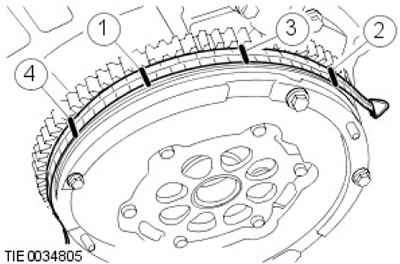
33.
NOTE: Rotate the crankshaft in the normal direction of rotation to the design position mark 50 degrees BTDC.
Install the special tool.
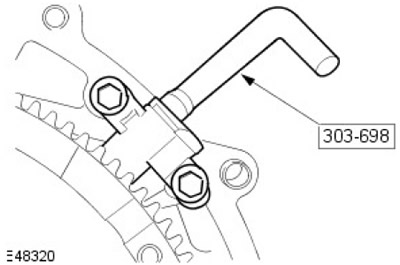
34. Attach the crankshaft position sensor bracket (CKP). Tighten the bolts to 23 Nm.
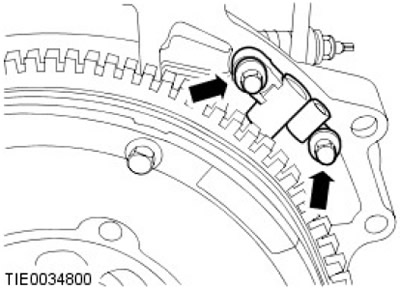
35.
NOTE: Clean the mating surface of the element.
NOTE: Measure the piston offset of each cylinder at TDC.
NOTE: The cylinder head gasket is selected by the largest measurement.
Measure the distance between the piston crown and the cylinder block at the indicated points.
- Use the table to determine the correct cylinder head gasket thickness.
For more information, please refer to the chapter: Specifications (303-01 Engine - Diesel engine ID4 2.4L, Specifications).
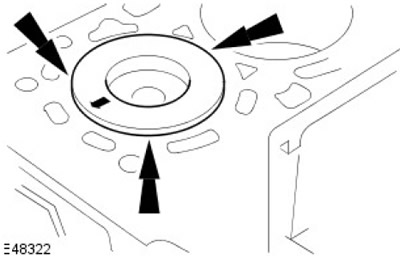
36.
CAUTION: The thickness of the new cylinder head gasket depends on the piston protrusion (marked hole/prong).
Install a new cylinder head gasket.
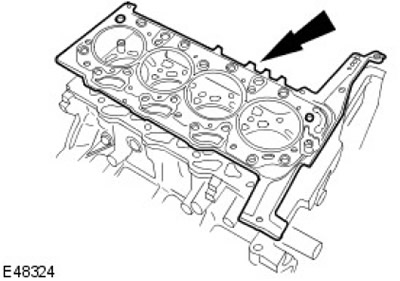
37.
CAUTION: Install new cylinder head bolts.
NOTE: Clean the mating surface of the element.
Install the cylinder head.
- Tighten the bolts in six steps in the sequence shown.
- Stage 1: Tighten bolts 1 to 10 to 20 Nm.
- Stage 2: Tighten bolts 11 to 18 to 10 Nm.
- Stage 3: Tighten bolts 1 to 10 to 40 Nm.
- Stage 4: Tighten bolts 11 to 18 to 20 Nm.
- Stage 5: Tighten bolts 1-10 180 degrees.
- Stage 6: Tighten bolts 11 - 18 180 degrees.
- Step 7: Tighten the M6 bolt to 10 Nm.
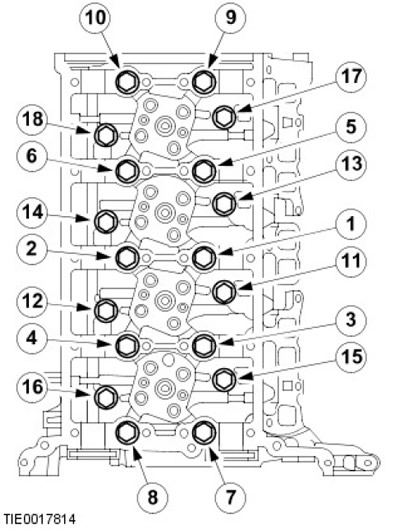
38.
NOTE: Clean the mating surface of the element.
Apply a bead of recommended sealant with a diameter of 2.5 mm to the cylinder head.
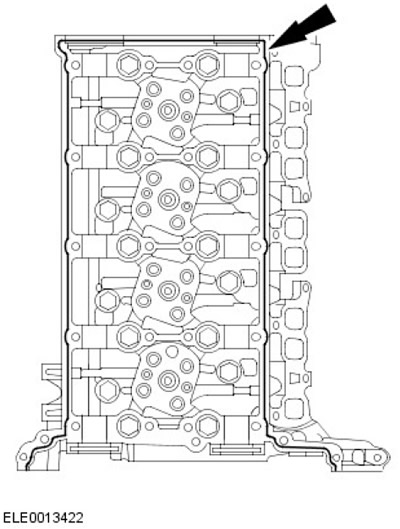
39.
NOTE: Clean the contact surfaces of the parts.
Install the camshafts. Lubricate the camshaft journals and cams with clean engine oil.
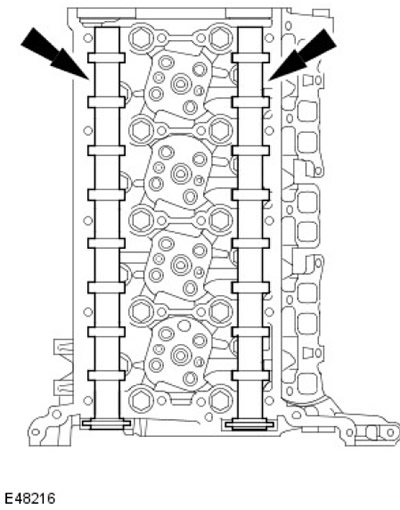
40.
NOTE: Tighten the bolts in two steps in the sequence shown.
Install the camshaft housing.
- Stage 1: Tighten bolts 1 to 22 to 23 Nm.
- Stage 2: Tighten bolts 23 to 25 to 10 Nm.
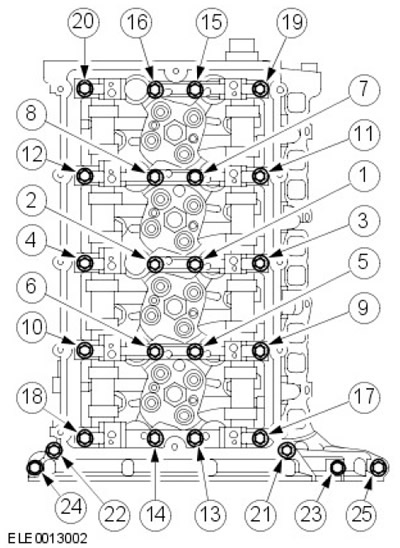
41. Using a suitable bar with a diameter of 6 mm, block the camshaft sprockets. Fit the camshaft sprocket bolts.
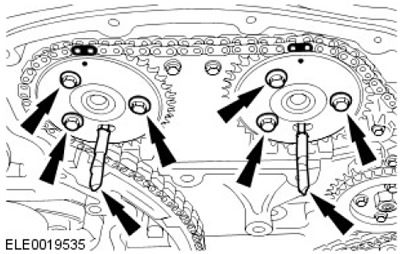
42.
Caveats:
- New bolts should be installed.
- Tighten the bolts in the order shown in the figure.
NOTE: Lubricate rocker shafts with clean engine oil.
NOTE: The oil supply holes in the rocker shafts must face down.
Install rocker shafts.
- Stage 1: Tighten the bolts (tightening torque 13 Nm).
- Stage 2: 45 degrees.
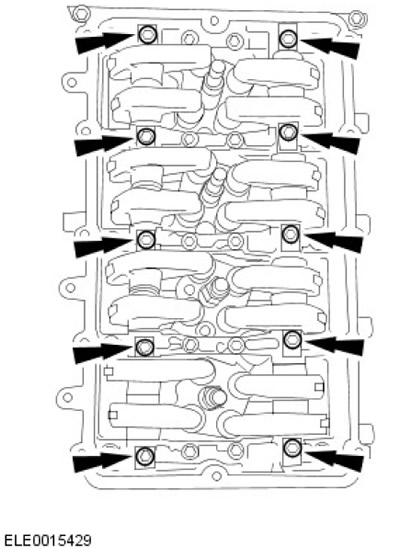
43. Install the high pressure fuel pump. Tighten the bolts (tightening torque 22 Nm).
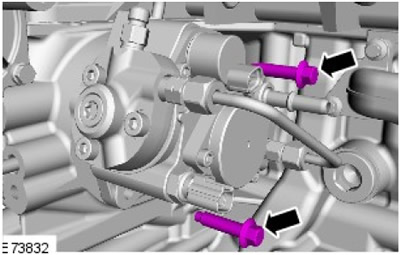
44.
NOTE: Do not tighten bolts at this stage.
Install the high pressure fuel pump sprocket. Screw in the bolts, but do not tighten them.
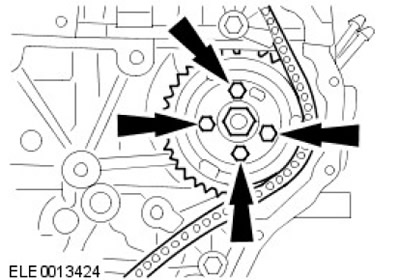
45.
CAUTION: Make sure the colored links are aligned with the alignment marks. Failure to do so may result in vehicle damage.
Install the timing chain.
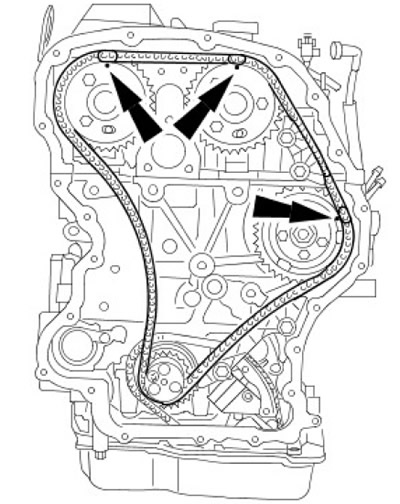
46.
CAUTION: Make sure the timing chain tensioner is fully retracted before installation. Failure to do so may result in vehicle damage.
Install the timing chain guides and tensioner.
- Tighten the bolts (tightening torque 15 Nm).
- tighten the nut (tightening torque 15 Nm).
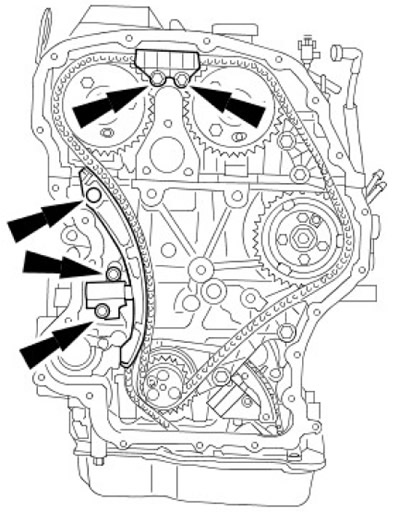
47. Unlock the timing chain tensioner. Unscrew the pin.
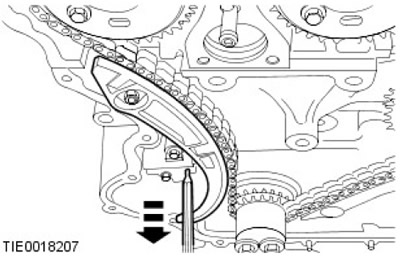
48. Tighten the intake camshaft sprocket bolt to 35 Nm.
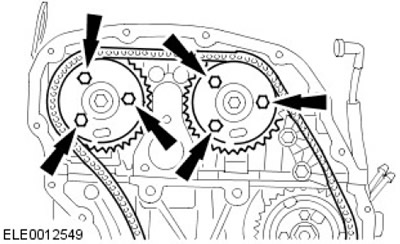
49. Tighten the injection pump sprocket bolts to 33 Nm.
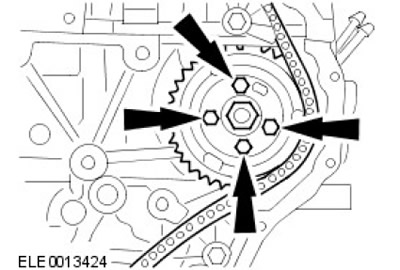
50. Remove the 6mm rods.
51. Remove special tools.
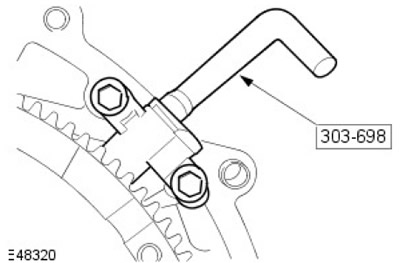
52. Turn the crankshaft clockwise 2 full turns.
53.
CAUTION: Make sure the special tool is properly installed on the flywheel.
Check the valve timing by inserting a special tool into the hole of the CKP sensor.
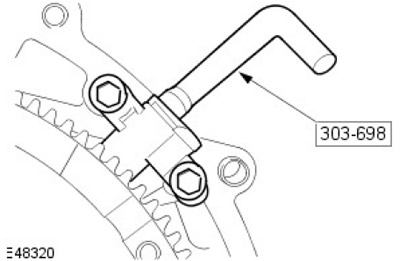
54. Check the timing of the camshaft by inserting a suitable bar with a diameter of 6 mm into the holes of the camshaft sprockets.
55. Remove special tools.
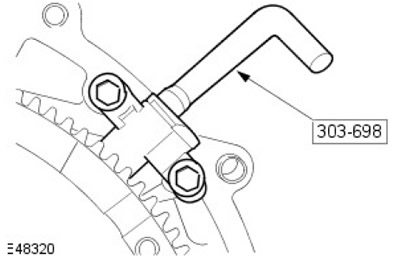
56. Remove the 6mm rods.
57.
NOTE: Clean the contact surfaces of the parts.
Using the special tool, install a new timing chain cover.
- Apply a bead of recommended sealant with a diameter of 3 mm to the timing chain cover.
- Tighten the bolts (tightening torque 14 Nm).
- Tighten nuts (tightening torque 10 Nm).
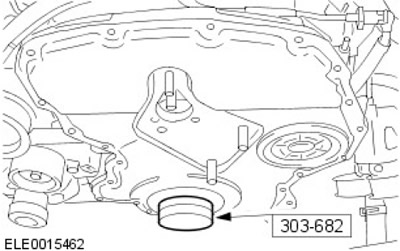
58. Remove special tools.
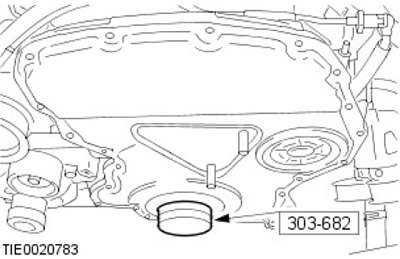
59.
NOTE: Install a new crankshaft front oil seal.
NOTE: A new crankshaft front oil seal is shipped with a locating sleeve that must be removed during installation.
Using the special tool, install the front crankshaft oil seal.
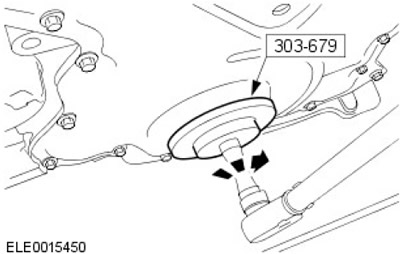
60.
Caveats:
- Tighten the bolts in the order shown in the figure.
- New bolts should be installed.
Install the crankshaft pulley.
- Stage 1: 45 Nm.
- Stage 2: 120 degrees.
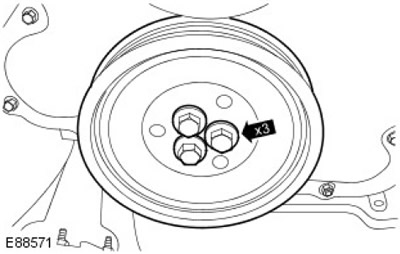
61.
NOTE: Install a new cylinder head cover gasket.
Install the cylinder head cover. Tighten the bolts (tightening torque 10 Nm).
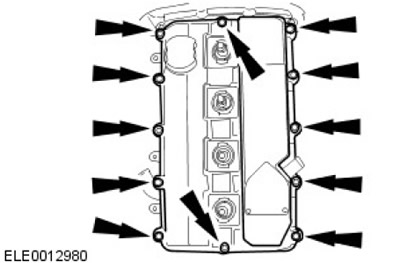
62. Install the SKR sensor. tighten bolt (tightening torque 7 Nm).
63.
NOTE: Clean the contact surfaces of the parts.
Install the cooling system outlet elbow to the cylinder head.
- Install the sealing ring.
- tighten the nut (tightening torque 22 Nm).
- Tighten the bolts (tightening torque 22 Nm).
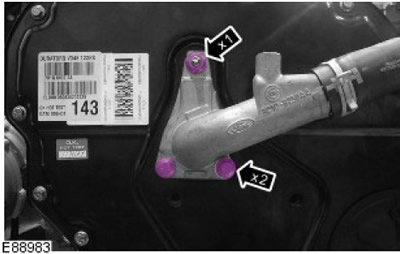
64. Install the accessory drive component bracket.
- Tighten the M10 bolts to 48 Nm.
- Tighten M8 bolts (tightening torque 22 Nm).
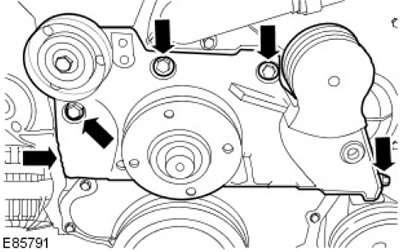
65.
CAUTION: At this stage, hand-tighten the bolts only.
Install the fuel manifold.
- Install the bracket.
- Screw in the bolts, but do not tighten them.

66. Install nozzles. Install new sealing washers.
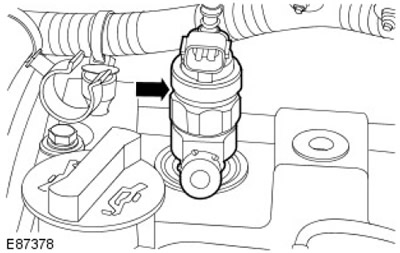
67.
Caveats:
- The injector clamp bolts may only be used twice.
- Tighten the bolts in the order shown in the figure.
Attach the nozzles.
- Install the injector clips.
- Stage 1: Tighten the bolts (tightening torque 6 Nm).
- Stage 2: 180 degrees.
- Install the injector clamp covers.
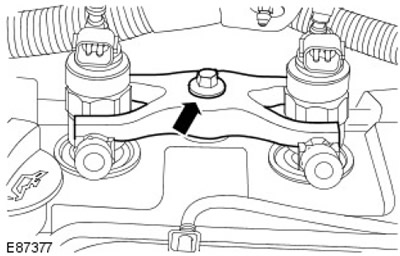
68.
CAUTION: Remove and discard plugs.
Connect the injector fuel return line. Install clamps.
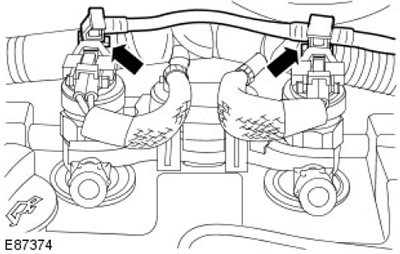
69.
Caveats:
- Apply pressure to the high pressure fuel supply line to keep the sealing lenses in contact with the cones of the fuel injectors and fuel rail when connected.
- Do not strike the sealing lenses of the high pressure fuel supply line, as this may damage the ends of the line and allow dirt to enter the fuel injection system.
- At this stage, tighten the connections by hand only.
NOTE: Remove and discard plugs.
Install new high pressure fuel feed lines.
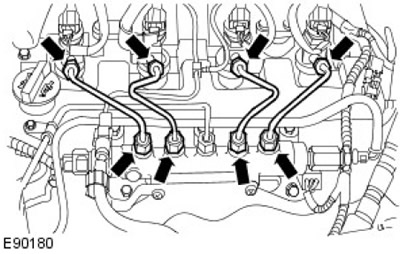
70.
Caveats:
- Tighten the high pressure fuel lines in the order shown in the figure.
- Remove and discard plugs.
Secure the high pressure fuel lines.
- Step 1: Tighten the high pressure fuel feed fittings on the fuel injectors and fuel pump to 35 Nm.
- Stage 2: Tighten the clamps of the high pressure fuel supply line to 10 Nm.
- Stage 3: Tighten the fuel rail bolts to 23 Nm.
- Step 4: Tighten the high pressure fuel feed line fittings on the fuel rail side to 35 Nm.
71. Install the engine wiring harness.
72. Connect the glow plug harness. Tighten nuts (tightening torque 2 Nm).
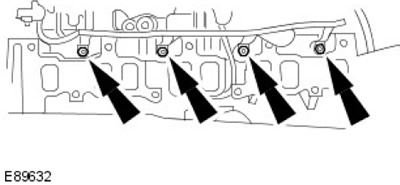
73. Attach the engine wiring harness support bracket.
- tighten the nut (tightening torque 10 Nm).
- Tighten the bolt to 10 Nm.
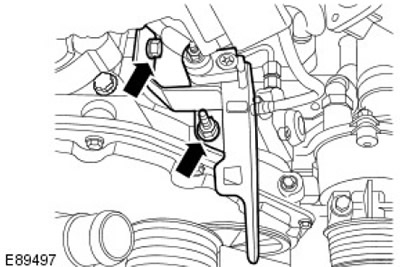
74. Connect the electrical connectors of the injectors.
- Attach the injector harness.
- Fasten with clamps.
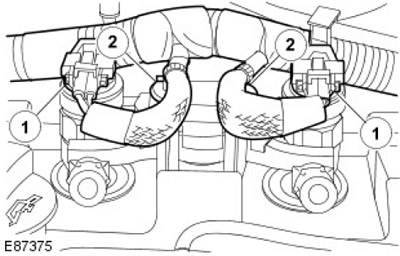
75. Connect the electrical connector of the pressure sensor in the fuel manifold (FRP).
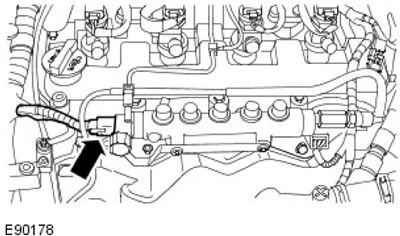
76.
NOTE: Check the correct location of the engine wiring harness.
Reinstall the engine cover. Tighten the bolts (tightening torque 10 Nm).
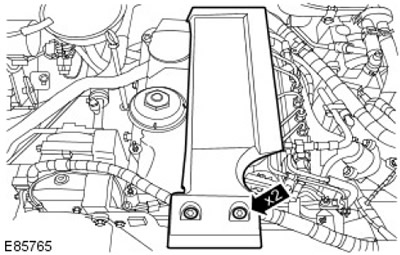
77.
CAUTION: Remove and discard plugs.
Install the turbocharger oil return line.
- Install the sealing ring.
- Install clamp.
- tighten bolt (tightening torque 22 Nm).
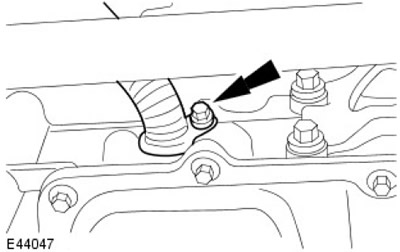
78. Establish an arm of the right support of the engine. Tighten the bolts (tightening torque 63 Nm).
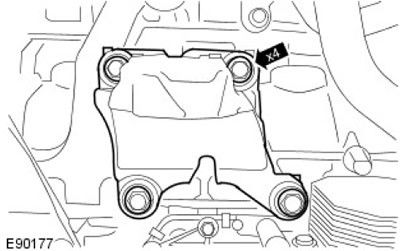
79.
CAUTION: New nuts must be used.
NOTE: Clean the contact surfaces of the parts.
Install the turbocharger assembly with the exhaust manifold.
- Install a new gasket.
- Tighten nuts (tightening torque 40 Nm).
- Tighten the bolts (tightening torque 40 Nm).
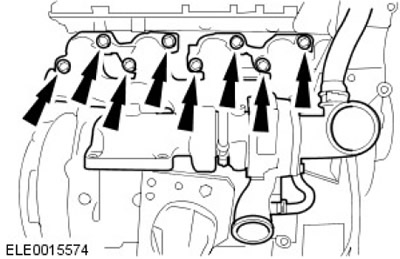
80. Attach the turbocharger oil return line.
- Install a new gasket.
- Tighten the bolts (tightening torque 10 Nm).
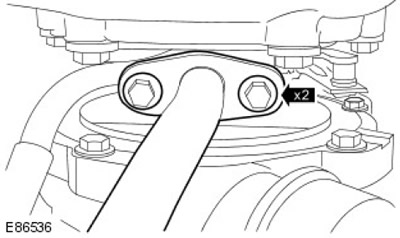
81.
CAUTION: Remove and discard plugs.
Insert the oil dipstick and install the oil level indicator tube.
- Install the sealing ring.
- tighten bolt (tightening torque 10 Nm).
- Fasten the wiring harness.
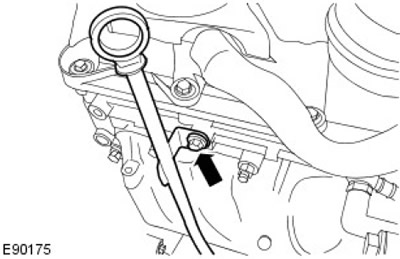
82.
CAUTION: Remove and discard plugs.
NOTE: Clean the contact surfaces of the parts.
Connect the turbocharger oil supply line.
- Install new sealing washers.
- Tighten the hollow bolt to 35 Nm.
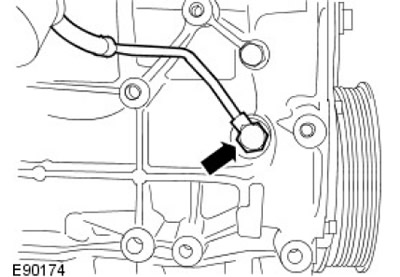
83. Connect the breather line. Lock the clamp.
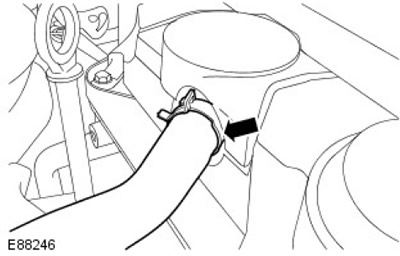
84. Connect the turbocharger drive electrical connector.
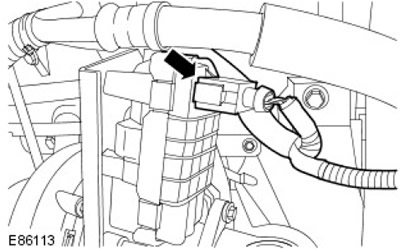
85. Fix the wiring harness of the mass air flow sensor (MAF). Fasten with a clamp.
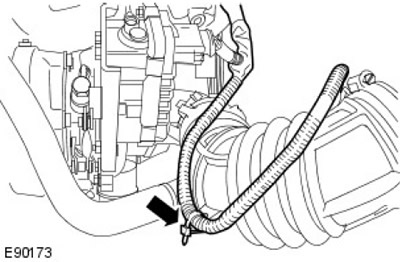
86. Install the generator support bracket. Tighten the bolts (tightening torque 25 Nm).
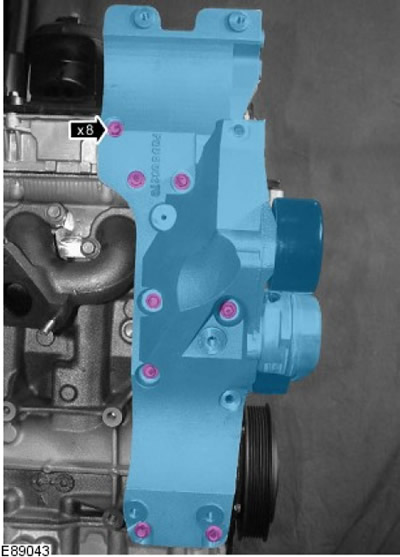
87. Install the turbocharger heat shield bracket.
- Tighten the M6 bolt to 10 Nm.
- Tighten M8 bolts (tightening torque 20 Nm).
88. Connect the generator. Tighten the bolts (tightening torque 48 Nm).
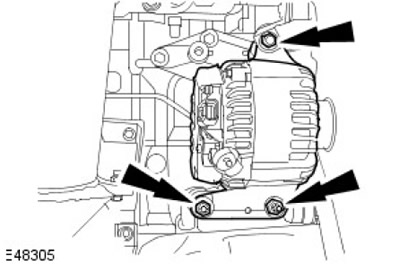
89. Connect the electrical connector of the generator.

90. Connect the positive battery cable to the alternator. tighten the nut (tightening torque 8 Nm).
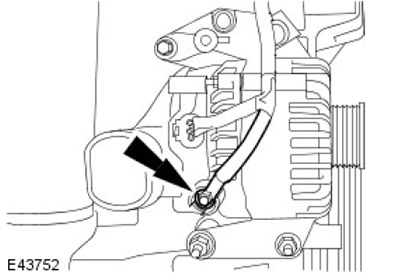
91. Install the A/C compressor. Tighten the bolts (tightening torque 22 Nm).
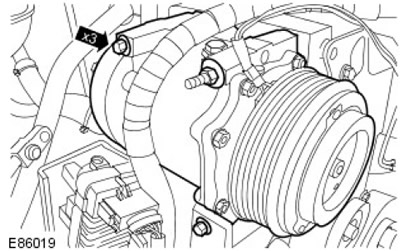
92. Connect the AC compressor electrical connector.
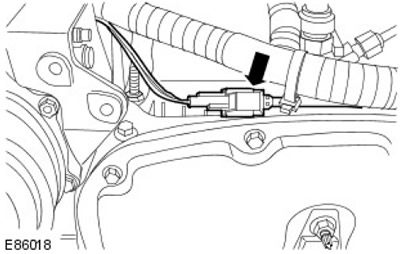
93. Install the engine lift bracket. Tighten the bolts to 10 Nm.
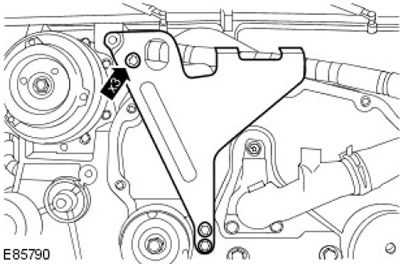
94. Install the A/C compressor pulley cover.
- Install the accessory drive belt to the A/C compressor pulley.
- Tighten the bolts to 10 Nm.
- tighten the nut (tightening torque 10 Nm).
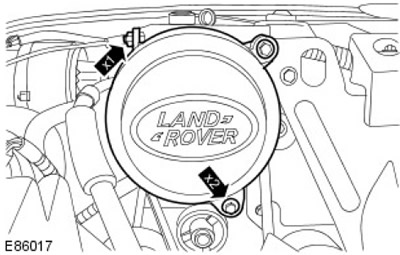
95.
CAUTION: Remove and discard plugs.
NOTE: Clean the contact surfaces of the parts.
Install the oil filter housing assembly.
- Install a new gasket.
- Tighten the bolts to 23 Nm.
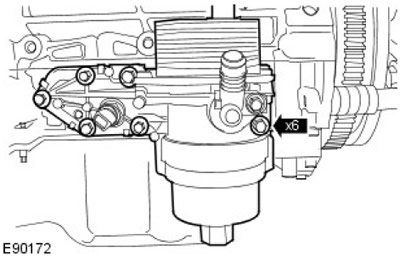
96. Install the left engine mount bracket. Tighten the bolts (tightening torque 63 Nm).
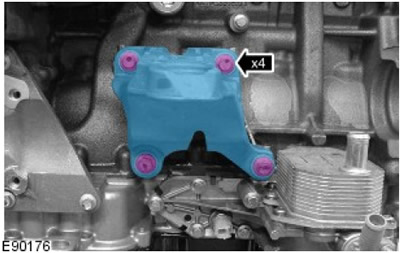
97. Install the power steering pump bracket. Tighten the bolts to 23 Nm.
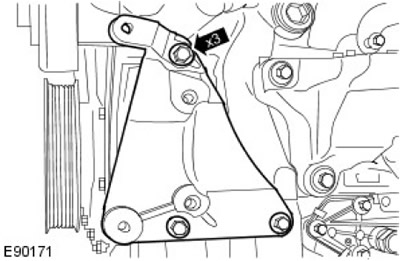
98. Install the coolant pump and coolant manifold assembly.
99.
NOTE: Clean the contact surfaces of the parts.
Attach the coolant pump.
- Install a new gasket.
- Tighten the bolts to 23 Nm.
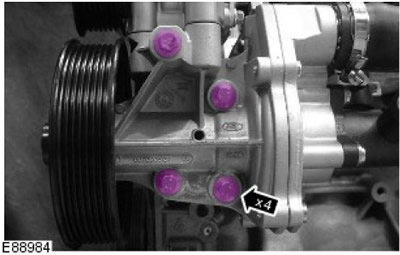
100. Attach the coolant manifold.
- Install a new gasket.
- Tighten the bolts to 10 Nm.
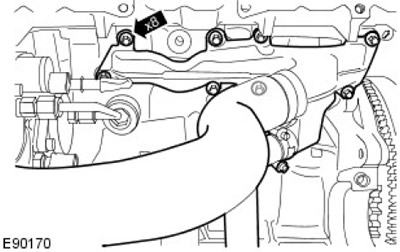
101. Connect the coolant hose. Lock the clamp.
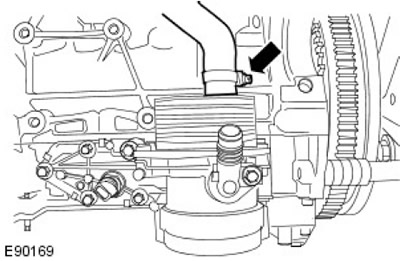
102. Connect electrical connectors for fuel metering valve and fuel temperature sensor.
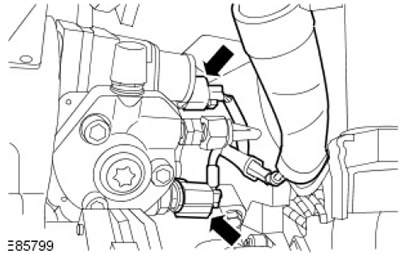
103. Connect the electrical connector of the engine oil pressure sensor (EOP).
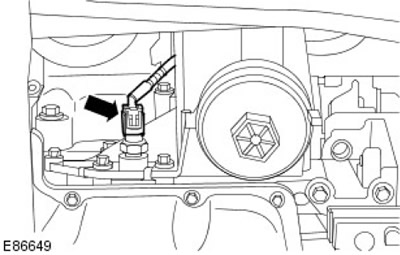
104. Attach the engine wiring harness. Secure with three clips.
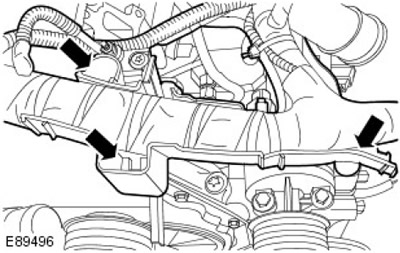
105.
NOTE: Clean the contact surfaces of the parts.
Install the exhaust pipe of the EGR valve (EGR) and intake manifold assembly.
- Install new intake manifold seals.
- Tighten the bolts (tightening torque 15 Nm).
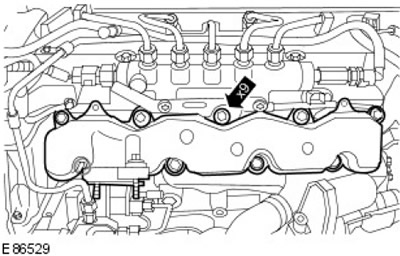
106. Attach the EGR valve outlet pipe. Tighten the bolt to 23 Nm.
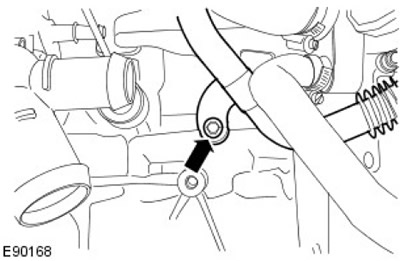
107.
CAUTION: Remove and discard plugs.
Install the high pressure fuel pump feed line. tighten bolt (tightening torque 7 Nm).
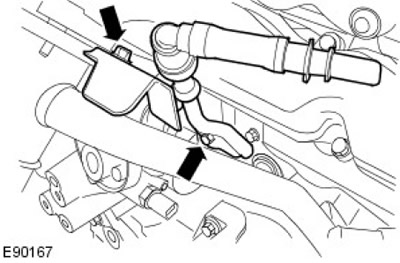
108. Attach the engine wiring harness.
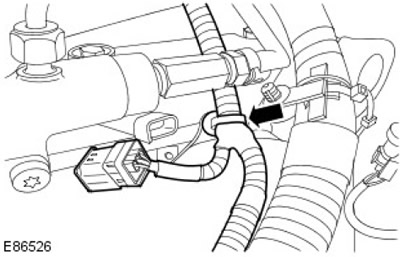
109. Connect the electrical connector of the camshaft position sensor (CMP).
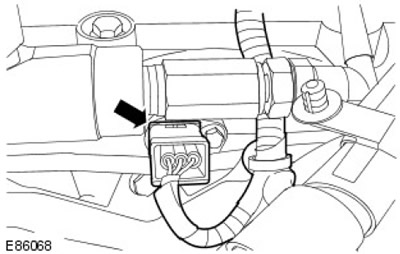
110.
NOTE: Clean the contact surfaces of the parts.
Install the EGR valve and EGR cooler.
- Install new gaskets.
- Tighten M8 bolts (tightening torque 23 Nm).
- Tighten M6 bolts (tightening torque 10 Nm).
- Connect the EGR valve electrical connector.
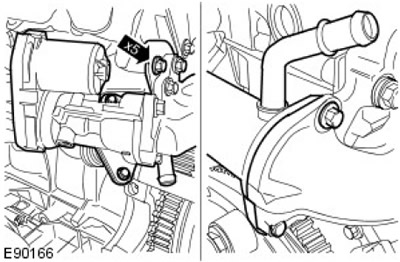
111. Connect the CKP sensor electrical connector.
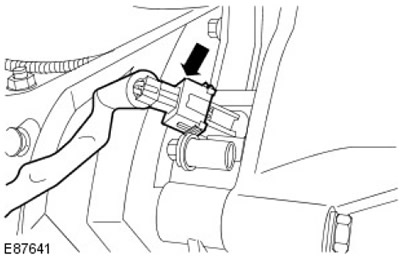
112. Remove the engine from the stand.
Comments on this article